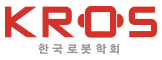
과채류 수확을 위한 로봇 엔드이펙터 리뷰
© Korea Robotics Society. All rights reserved.
Abstract
Fruit and vegetable harvesting robots have been widely studied and developed in recent years to reduce the cost of harvesting tasks such as labor and time. However, harvesting robots have many challenges due to the difficulty and uncertainty of task. In this paper, we characterize the crop environment related to the harvesting robot and analyzes state-of-the-art of the harvesting robot especially, in the viewpoint of robotic end-effector. The end-effector, an one of most important element of the harvesting robot, was classified into gripper and harvesting module, which were reviewed in more detail. Performance measures for the evaluation of harvesting robot such as test, detachment success, harvest success, and cycle time were also introduced. Furthermore, we discuss the current limitations of the harvesting robot and challenges and directions for future research.
Keywords:
End-effector, Harvesting, Robot, Gripper, Cutting, Grasping1. 서 론
전세계적으로 인구가 증가하고 있으며, 점진적으로 증가되 는 인구에 대한 식량 문제를 해결하기 위해서 작물 생산량 증 대가 필요한 시점이다. 하지만, 현재 농업의 형태로는 인구고 령화, 노동력부족, 기후변화, 농촌인구 감소, 토양의 황폐화, 도시화로 인한 농촌토지 감소 등의 이유로 오히려 생산량이 감소할 수 있다. 이를 극복하기 위해 농업은 4차산업혁명을 맞 이하여 빅데이터(Big data), 인공지능(AI), 로봇(Robot), 사물 인터넷(IoT), 정보통신기술(ICT)를 활용하여 효율적인 농작 물 관리와 생산량 향상을 도모하고 있으며 정밀농업과 스마트 농업 활성화에 힘쓰고 있다[1].
현재의 농업은 생산량 향상과 더불어 품질, 제품의 다양성 등에 대한 요구에 직면해 있다. 이는 생산 과정을 개선해야만 하며, 일반적으로 수확 비용을 상승시킨다. 비용은 단순한 가 격적인 측면뿐만 아니라 가장 중요한 노동력 또한 포함되며 로봇화, 자동화를 통한 생산 방식은 비용증가와 그에 따른 이 윤감소를 초래할 수 있다.
과실을 획득하기 위해서 이식, 접목, 방제, 파종, 수확, 가지 치기 등 다양한 작업이 진행되며 그 중 수확작업은 일본농업 의 경우 25%를 차지할 정도로 많은 시간과 노동이 투자된다. 수확작업의 비용(시간, 노동력)절감을 위해 수확작업의 로봇 화, 자동화에 많은 연구가 진행되었지만, 노력에도 불구하고 지난 30년간 상용화에 성공하지 못했다[2].
수확로봇의 주요 연구에는 작물에 대한 색상, 크기 및 모양 등에 대한 인식을 위한 영상처리 기술[3], 엔드이펙터[4], 매니퓰 레이터 자세 제어기술[5], 그리퍼 구동 메커니즘[6]이 있다. 이 중 엔드이펙터는 대상 작물에 직접적인 작업을 수행하기 때문 에 엔드이펙터의 특성에 따라 수확 과정 중 주변 줄기, 과실에 대한 손상 등이 발생할 수 있다. 즉, 수확로봇 성능에 가장 큰 영향을 줄 수 있는 요소이므로 본 논문에서는 수확로봇 엔드 이펙터의 연구개발에서 주로 다루는 그리퍼, 수확모듈에 대한 내용에 중점을 둔다.
본 논문의 구성은 다음과 같다. 2장에서는 작물의 재배환경 에 대해 설명하고, 3장에서는 조사된 수확로봇의 성능을 평가 지표로써 정리하였다. 4장에서는 엔드이펙터에 대한 주요기 술과 동향을 서술한다. 5장과 6장에서는 수확로봇의 한계 및 도전과제에 대해 고찰하고 본 연구의 내용을 요약한 후 결론을 맺는다.
2. 재배 환경
수확 로봇 설계 및 제작을 위해 수확 대상인 작물의 특성과 로봇의 작업이 이루어지는 환경을 파악하는 것이 중요하다. 작물은 과수원, 시설원예 등 다양한 환경에서 재배되며, 각각 의 작물마다 크기, 위치, 모양, 재배방법, 수확방법 등이 다르 다. 또한 재배환경에서 이루어지는 수확 과정 중 작물을 인식 하는 과정이나 수확로봇이 이동하는 과정에서 장애물이 되는 다양한 물체들(canopy, 구조물)이 많이 존재한다. 수확로봇에 영향을 주는 작물의 특성과 환경에 대한 요인, 수확방법들을 충분히 고려하여 수확 로봇을 설계 및 제작해야 한다.
작물을 재배하는 환경에는 [Fig. 1]과 같이 과수원, 시설원예, 노지환경으로 크게 세 가지가 있다. 사과, 오렌지, 키위처럼 큰 나 무에서 자라는 작물들은 주로 과수원에서 재배되고 비교적 작은 줄기에서 자라는 작물들은 시설원예, 노지환경에서 재배된다.
![[Fig. 1] [Fig. 1]](/xml/26081/JKROS-15-2-91_F1.jpg)
Production environments according to crops: (A) apple in orchard[6], (B) sweet pepper in horticulture[4], (C) mushroom in horticulture[2], and (D) watermelon in open field[2]
수확로봇에 대한 영향을 주는 요인은 작업이 이루어지는 재 배환경에 따라 차이점이 존재한다[2]. 과수원과 노지환경은 시 설원예와 달리 비와 바람의 영향을 많이 받는다. 또한 플랫폼 의 이동 용이성이 떨어지고 작물의 일관성이 떨어진다. 그리고 시설원예는 나머지 재배환경과 달리 광 조건을 제어할 수 있다 는 이점과 비교적 장애물이 적기 때문에 작물에 대한 가시성과 접근성이 더 높다. 결론적으로 재배환경 중에서 시설원예가 수 확로봇을 사용하여 작업을 수행하기에 가장 적합한 환경이다.
세 가지 재배 환경에서 재배되는 작물들의 수확 로봇을 조 사하여 [Table 1]과 같이 정리하였다. 조사 결과 21개의 수확 로봇이 개발되었다. 재배 환경을 기준으로 비교하였을 때 시 설원예 71.5%, 과수원 19%, 노지환경 9.5%로 시설원예에서 재배하는 작물의 수확 로봇이 가장 많았다. 또한 작물을 기준 으로 비교했을 때 토마토 수확 로봇, 딸기 수확 로봇 19%(4개, Horticulture), 파프리카 수확 로봇 14%(3개, Orchard)로 토마 토, 딸기, 파프리카를 대상으로 한 수확 로봇이 많았다.
3. 평가지표
조사한 문헌에 보고된 측정데이터를 기반으로 평가 지표를 정의하였다. Test, Detachment Success, Harvest success, Cycle time 총 4가지의 지표로 설명하였다.
‘Test’는 실험을 진행하는 장소를 Field와 Lab으로 구분한 지표이다. 자체적으로 실내 테스트베드를 구축하여 실험을 진 행한 Lab 실험은 실제환경에서 고려돼야 할 환경변수들이 충 분히 구축되지 않아 이상적인 실험결과를 나타낸다. Field 실 험을 진행하여야 실질적인 수확로봇 성능을 검증할 수 있다.
‘Detachment success[%]’는 주변 환경에 대한 손상이 고려 되지 않은 지표로, 줄기로부터 성공적으로 과실을 수확한 정 도이다. 주변 과실과 장애물에 대한 충돌을 회피하기 위한 행 동 계획의 성능을 보일 수 있는 지표이며, 엔드이펙터와 과실 간의 상호작용을 측정할 수 있다.
‘Harvest success[%]’는 줄기로부터 분리된 과실이 손상없이 성공적으로 수확된 과실의 정도이다. 이 지표는 과실의 올바른 수확 시기, 주변 환경에 대한 손상도 등 수확로봇의 전체적인 성능에 관련이 있으며, 현재 보고된 수확 성공률은 각 연구마다 기준이 상이하여 수치상으로 비교하기엔 어려움이 존재한다.
‘Cycle time[1EA/s]’은 과실 수확 평균 작업 시간으로 과실 의 인식(숙도 판별, 위치 추정), 수확, 운송작업이 포함되지만, 연속적으로 진행하는 수확과정에서 다음 과실로의 접근 시간 을 제외하여 측정되었다. 이 지표는 로봇의 도입을 위해 고려돼 야 하는 사항으로 로봇의 경제성을 판별할 수 있는 지표이다.
4. 엔드이펙터
엔드이펙터는 로봇이 작업을 할 때 작업 대상에 직접 작용 하는 기능을 가진 부분으로 수확용으로 사용될 뿐만 아니라 산업용, 의료용 등 다양하게 사용된다. 그 중 수확용 엔드이펙 터는 작업환경의 복잡성, 조작 대상의 불규칙성으로 인해 정 확하고 유연성을 필요로 하며[3], 작물의 다양한 특성에 맞춰 연구 및 설계가 진행되고 있다[6].
수확 로봇의 중요한 구성 요소인 엔드이펙터는 과채류를 수 확하는 과정에서 결정적인 역할을 수행한다. 수확로봇의 성능 을 향상시키기 위해서는 과채류의 수확속도를 높이거나 수확 성공률 향상을 도모해야 한다. 또한, 과실에 대한 손상없이 수 확할 수 있어야 하기 때문에, 과실의 특성에 맞춰 [Fig. 2], [Table 2]와 같이 다양한 형태로 개발되었다. 즉, 수확로봇의 성능은 엔 드이펙터의 특성과 밀접한 관련이 있다[8]. 조사된 엔드이펙터 의 그리퍼 및 수확모듈의 특징에 대해 [Table 2]로 정리하였다.
![[Fig. 2] [Fig. 2]](/xml/26081/JKROS-15-2-91_F2.jpg)
Research and development in harvesting of fruit and vegetable end-effector with different manipulator and gripper design for: (A) apple[6], (B) citrus[8], (C) strawberry[14], (D) cucumber[21], (E) sweet pepper[20], (F) tomato[11], (G) mushroom[22], (H) asparagus[25]
4.1 그리퍼
수확용 엔드이펙터의 구성요소 중 하나인 그리퍼는 단단한 재료를 이용하여 제작한 그리퍼로 연구 개발되었다[24,26]. 특정 작물에 적용하기 위해 작물이 갖는 물성치를 고려하여 설계되 었다. 단단한 재료를 갖는 그리퍼는 보다 강하게 파지할 수 있 으나, 물체를 접촉하면 충격이 발생하여 물체가 손상되거나 원하는 경로 밖으로 밀려날 수 있는 단점이 존재한다[27]. 단순 한 해결 방안으로 그리퍼 접촉부분에 고무패드 등의 적합한 재료를 추가하는 것이다. 대상작물에 대한 정확한 위치를 필 요로 하며 만약 정확한 위치를 파악할 수 없다면 줄기로부터 작물을 분리할 때, 그 작물이 파손되거나 식물의 핵심줄기를 자르거나 손상을 입힐 수 있다.
두 번째 방법은 소프트로봇 기술을 응용한 소프트 그리퍼 를 제작하는 것이다. 이 방식은 최근에 활발히 연구가 계속되 고 있는 방식으로 유연한 재료를 사용함에 따라, 대상작물에 대한 손상을 최소화하고, 작물의 특성인 비정형성을 극복할 수 있는 장점을 갖고 있어 과채류 대상으로 적용하고 있다[28,29]. 또 한, 재료가 갖는 유연성에 의해 물질이 변형되기 쉬워 제어 복 잡성이 크게 줄어든다[27]. 하지만 이 그리퍼 또한 작물을 직접 잡는 방식이므로 정확한 위치를 요구하는 단점이 있다.
[Fig. 3]과 같은 진공 방식의 흡착 컵(suction cup)을 활용한 소프트 그리퍼는 한 줄기에 군집(cluster)을 이루며 자라는 작 물을 수확할 때 효과적이고 위의 두 방식보다는 정확한 위치 를 필요로 하지 않는다. 하지만 강한 흡착력으로 인해서 작물 에 손상이 가해질 수 있고 크게 굴곡져있는 작물은 흡입하기 어려울 수 있으며, 장시간 파지가 힘들다는 단점이 존재한다.
[Fig. 2]의 딸기 엔드이펙터[14]는 파지 시 발생가능한 표면 손상을 방지하기 위해 줄기를 파지하여 수확하는 방법으로 접 근하였다. 흡착 파지와 비흡착 파지 2가지 형태로 엔드이펙터 의 성능을 비교하였으며, 흡착 파지 방법은 과실이 고정되어 3 차원 위치 오차가 보상되는 장점을 보였다. 하지만 흡착을 사 용한 파지는 과일의 흔들림 감소에는 효과적이였지만, 흡착 파지 시 파지실패율은 15.4%, 비흡착 파지 시 14.4%로 유의미 한 차이를 보이지 않아 파지 성능에 크게 기여하지 않았다.
[Fig. 2]의 토마토 엔드이펙터[11]는 핑거에 고무를 부착하여 과실의 표면 손상을 방지하고, 흡착 컵을 사용하여 파지 영역 으로 끌어당긴 후 핑거로 2차 파지를 수행하였다. 파지영역을 확보하여 파지 시 발생가능한 주변환경과의 충돌을 방지하였 으며, 흡착 컵을 파지 보조수단으로 두어 그리퍼 성능을 향상 시켰다. 흡착 컵의 직경과 과실의 크기, 무게에 따른 흡착 성공 률을 실험을 통해 최적의 흡착 컵 직경을 설계하여 파지능력 향상과 과실의 손상을 최소화하였다.
4.2 수확모듈
엔드이펙터에 사용되는 절단 시스템은 작물, 플랫폼에 따 라 다양하게 사용되고 있는데 대표적으로는 칼날을 사용한 방 식과 사용하지 않는 방식으로 분류할 수 있다. 먼저 칼날을 사 용하지 않는 방식은 매니퓰레이터를 비틀거나, 엔드이펙터를 회전하는 방식으로 작물을 줄기(peduncle)로부터 분리하는 방 식이다. 토마토 수확 엔드이펙터 중 하나로 [Fig. 4]와 같이 적 용되었으며[30] 무한회전 조인트의 회전을 통하여 과실을 수확 하였다. 칼날을 이용한 방식은 칼날에 정확히 줄기를 넣어야 하기 때문에 줄기 추정의 정확도를 요구하는 반면, 회전을 통 한 수확 메커니즘은 줄기 방향을 고려하지 않고 수확을 할 수 있어 추정오차에 강인한 방법이다. 하지만, 실제 어플리케이 션에서 줄기로부터 과실분리 성공률은 62.2%로 비교적 낮은 성공률을 보였다.
![[Fig. 4] [Fig. 4]](/xml/26081/JKROS-15-2-91_F4.jpg)
(a) tomato harvesting robot system (left), image of rotational plucking mechanism (right), (b) harvesting in horticulture[30]
엔드이펙터의 절단부 중 한 방법은 [Fig. 5]와 같이 두 개의 전극을 니크롬선으로 연결한 후 발생하는 고온의 아크를 이용 해서 줄기와 과실을 분리하는 방법으로 파프리카, 오이를 대 상으로 개발되었다. 고온의 열을 이용해서 절삭하기 때문에 일반적으로 가위로 절단하는 것과 비교하여 바이러스나 곰팡 이 등의 감염을 지연시키거나 줄일 수 있는 장점을 보였다[19]. 오이 수확로봇은 오이를 잡기위한 흡착 컵이 있는 그리퍼와 열 절단 장치로 과실을 줄기로부터 분리시키는 방식의 엔드이 펙터로 개발되었다. 시설원예 내에서 실험이 진행되었으며, 평균 45초의 속도와 80%의 수확성공률을 보였다.
![[Fig. 5] [Fig. 5]](/xml/26081/JKROS-15-2-91_F5.jpg)
Thermal cutting system, (a) electric arc thermal cutting system, (b) temperature thermal cutting system[19]
칼날을 사용한 방식의 예로서, 수확로봇의 대표적인 프로 젝트인 CROPS는 파프리카를 대상으로 2가지 타입의 엔드이 펙터를 개발했다[31,32]. 2가지 타입의 파프리카 수확로봇은 RGB 및 ToF (Time of Flight) 이미지를 기반으로 과실의 숙도 판별 및 위치추정을 수행하였다. 추정된 위치에 대한 자세추 정을 통해 수확작업을 진행하였다. 장착된 카메라의 시점에서 발생하는 행동계획의 문제를 해결하기 위해 매니퓰레이터는 중앙 작업공간으로 이동하여 작업을 진행하였다.
[Fig. 6]의 Fin-Ray 타입의 엔드이펙터는, 4개의 핑거를 사 용하여 파프리카를 파지 후, 위쪽에 존재하는 가위를 사용하 여 수확하는 방식이다. 핑거는 열가소성 탄소체(TPE)를 사용 하여, 재료가 갖는 탄성을 이용해 수확물의 불규칙적인 모양 에 적응할 수 있도록 개발되었다. 수확과정 중 줄기와 과실과 의 간격이 좁은 경우 주변 잎, 줄기에 대한 손상이 발생하였다. 하지만 수작업으로 수확을 진행하여도 발생하는 문제로 큰 영 향이 없을 것으로 판단하였다.
[Fig. 7]은 Lip-type의 엔드이펙터로 중앙에 존재하는 흡착 컵을 매니퓰레이터의 tool center point (TCP)로 두어, 1차로 파 프리카를 파지 후 위 아래 Lip에 부착된 칼날을 이용하여 줄기 를 절단한다. 아래 Lip의 움직임으로 수확이 이뤄지며 이와 동 시에 하단에 부착된 튜브를 통해 이송하는 방식이다. 수확 후 운송시간을 줄임으로써 수확속도를 향상시켜 수확로봇의 성 능을 높이고자 하였다.
![[Fig. 7] [Fig. 7]](/xml/26081/JKROS-15-2-91_F7.jpg)
(a) Lip-type end-effector front view, (b) the flexible tube attached to the end-effector for guiding the fruit to the storage container, and (c) Lip-type end-effector fruit detachment sequence[31]
최근에 이뤄진 연구에 따르면 과실을 수확하기위한 비용 (시간)을 줄이기 위하여 파지를 수행하지 않고 수확하는 방식 의 엔드이펙터를 개발하였다[4]. 작물환경을 최적의 상태로 구 축하였을 때와 평상시 작물환경에서 수확로봇을 도입하였을 때를 비교하여 수확로봇의 성능에 작물의 환경이 미치는 영향 을 실험을 통해 유의미한 차이를 보였다.
딸기 수확용 로봇은 위치 추정에 대한 오차와 군집을 이루 며 자라는 작물에서 특정 대상을 분리하기 위해 cable-driven 방식의 그리퍼를 갖는 엔드이펙터를 개발하였다[17]. 줄기의 위치 추정은 특정 대상의 줄기뿐 아니라 주변 줄기와 특징을 분리하기 어려워 목표 줄기의 추정이 어려운 환경이므로, 과 실의 위치추정에 중점을 두어 진행하였다. 강인한 위치추정을 기반으로 잡아 삼키는 방식의 파지를 수행하였고, 굽은 칼날 로 줄기를 절단하여 줄기 위치 추정에 중점을 둔 다른 수확로 봇에 비해 수확 성능 향상의 효과를 보였다[Fig. 8].
![[Fig. 8] [Fig. 8]](/xml/26081/JKROS-15-2-91_F8.jpg)
(a) strawberry harvesting end-effector design, (b) harvesting sequence of active obstacle separation: front obstacle, side obstacle (green berries), and bottom obstacle[33]
또한 작업성능을 높이기 위하여 지속적으로 연구가 이뤄지 고 있으며, 다수의 매니퓰레이터를 적용하였다. 각각의 매니퓰 레이터에 대해 작업영역을 나누고, 작업영역을 할당하여 실험을 진행하였다[33]. 이는 수확로봇의 강한 협업(strong cooperation)이 필요한 작업은 아니며, 각각의 수확로봇이 할당된 영역에서 수 확을 수행하여 전체 작업의 시간을 줄임으로써 수확작업의 효율 성 증가를 기대한다. 또한 나눠진 작업영역에 대해 작업을 수행 하기 때문에 매니퓰레이터간 충돌방지를 기대할 수 있다.
5. 고찰 및 도전과제
5.1 한계
농업은 작업환경에 대한 복잡성, 작물의 불규칙성으로 인 해 로봇 조작의 한계가 드러나며, 작물의 물성치를 고려해야 하므로 아직까지는 특정 작물에 대한 수확용 엔드이펙터의 개 발이 이뤄졌다[8,18]. 소프트 그리퍼의 연구가 진행됨에 따라 다 양한 작물에 대해 파지 가능한 그리퍼를 적용할 수 있지만, 각 작물마다 수확방법이 다르다. 군집을 이루며 자라는 작물의 경우 목표작물을 주변 장애물로부터 섬세하게 분리하기에는 큰 형태일 수 있으며, 작은 엔드이펙터의 경우 큰 과일을 파지 할 수 없어 이 문제점을 해결해야한다[33]. 또한 수확을 위해선 줄기로부터 과실을 분리하는 것이 중요하지만, 다양한 작물에 대한 적용가능한 수확모듈은 현재로서는 힘든 단계이다.
현재 연구, 개발된 엔드이펙터는 자체 실험 등에서는 우수 한 수확성공률을 보이나 실질적인 현장실험을 진행하지 않아 수확성능을 보장하기 힘들다. 대다수의 현장실험은 평가된 표 본 수가 충분하지 않고 특정 기간에 대해서 실험이 이뤄졌기 때문에 로봇 기반의 수확 작업이 수작업으로 수확하는 방법에 비해 어느 정도 성능을 보이는지 확신할 수 없다. 작물환경은 외부요소의 변화와 더불어 시간의 경과에 따른 작물의 상태 등에 따라 항상 변할 수 있으므로, 수확 로봇의 성능이 달라질 수 있다. 따라서, 광범위한 조건에서 실험을 하여 로봇의 성능 을 입증할 필요성을 보인다.
5.2 평가지표
수확로봇의 성능을 검증하기 위해서는 명확한 성능지표가 필요하다. 수확로봇의 성능을 판별하기 위해 수확속도, 수확 성공률 뿐만 아니라 수확과정 중 발생하는 과실에 대한 손상 과 식물에 발생하는 손상도 또한 명확한 기준으로 판별해야 한 다. 식물에 대한 손상은 주변 작물의 질병을 초래할 수 있으며, 이는 수확량 감소 등을 유발하기 때문에 수확로봇의 성능을 판 별함에 있어 고려해야 할 상황이다. 하지만 작업환경, 작물환 경에 따라 모든 작업이 같은 형태를 보이지 않아 수치화하기 어려울 수 있으며 불분명하고 모호한 각 연구별 상이한 기준은 수확로봇의 성능을 비교 및 판별하기에 어려움이 존재한다.
5.3 다중 수확로봇
지금까지의 수확로봇은 다양한 방법으로 수확성능을 높이 고자 하였으나 작업의 어려움, 불확실성의 영향으로 높은 성 능을 보이지 못했다. 지속적인 연구를 통해 일정수준의 성능 을 보인다면, 다수의 수확 로봇을 사용하여 동시다발적으로 작업을 진행하여 작업완료 시간을 단축을 통한 작업효율 향상 을 기대할 수 있다. 하지만 각각의 수확로봇의 작업공간을 정 의하고, 경로계획[6,34], 행동계획[35], 작업계획[36]이 충분히 고 려돼야 장애물 회피, 로봇 간 충돌 방지할 수 있다. 현재로서는 단일 로봇의 행동계획에 대한 연구가 많이 진행되고 있다. 다 수의 수확로봇을 활용한 연구가 진행되고 있으나[33] 그 수가 많지 않아 많은 연구가 이뤄진다면 수확용 로봇에 큰 변화를 가져올 수 있을 것으로 기대한다.
또한 매니퓰레이터의 협업을 통해 절단을 담당하는 한쪽 매니퓰레이터가 주변 canopy를 제거하고, 다른 한쪽의 매니퓰 레이터는 수확을 담당하여 두 매니퓰레이터 간의 협력을 통해 최적의 수확환경(작업하기 쉬운 환경, 매니퓰레이터의 자세 제어를 통한 수확 자세 최적화 등)을 구축하는 시스템을 고려 해볼 수 있다. 이는 보다 정밀한 영상처리를 기반으로 매니퓰 레이터의 협업을 통해 목표로 하는 수확 작물 이외의 장애물 을 제거하는 방식으로 작업이 진행되어질 수 있다. 전체 작업 시간이 증가할 수 있으나, 높은 수확 성공률을 보일 것으로 예 상된다.
6. 결 론
과채류 수확로봇 엔드이펙터는 지속적으로 연구 개발이 진 행되고 있으나 작업의 어려움, 불확실성으로 인해 많은 해결 과제가 남아있다. 본 논문에서는 수확로봇의 핵심인 엔드이펙 터의 그리퍼와 수확모듈에 대한 최근 동향을 살펴보았다. 또 한 다양한 작물 환경에 대해 연구개발되고 있는 대표적인 수 확용 엔드이펙터를 소개하였으며 향후 수확용 엔드이펙터의 개발에 있어 해결 및 도전과제에 대해서 기술하였다. 연구가 지속됨에 따라 머지않아 상용화 수준의 수확용 엔드이펙터가 개발되어 질 것으로 예상되며 미래농업의 핵심적인 역할을 할 것으로 기대한다.
Acknowledgments
This research was supported in part by the Technology Innovation Program (20004055) funded by the Ministry of Trade, Industry & Energy (MOTIE), and in part by X-mind Corps program of National Research Foundation of Korea(NRF) funded by the Ministry of Science, ICT (2019H1D8A110967311)
References
-
J. Kim, S. Kim, C. Ju, and H. I. Son, “Unmanned aerial vehicles in agriculture: A review of perspective of platform, control, and application,” IEEE Access, vol. 7, pp. 105100-105115, 2019.
[https://doi.org/10.1109/ACCESS.2019.2932119]
-
C. W. Bac, E. J. van Henten, J. Hemming, and Y. Edan, “Harvesting robots for high-value crops: State-of-the-art review and challenges ahead,” Journal of Field Robotics, vol. 31, no. 6, pp. 888-911, 2014.
[https://doi.org/10.1002/rob.21525]
-
X. Zou, M. Ye, C. Luo, J. Xiong, L. Luo, H. Wang, and Y. Chen, “Fault-tolerant design of a limited universal fruit-picking end-effector based on vision-positioning error,” Applied Engineering in Agriculture, vol. 32, no. 1, pp. 5-18, 2016.
[https://doi.org/10.13031/aea.32.10701]
-
B. Arad, J. Balendonck, R. Barth, O. Ben-Shahar, Y. Edan, T. Hellström, J. Hemming, P. Kurtser, O. Ringdahl, T. Tielen, and B. van Tuijl, “Development of a sweet pepper harvesting robot,” Journal of Field Robotic, 2020.
[https://doi.org/10.1002/rob.21937]
-
C. Lehnert, A. English, C. McCool, A. W. Tow, and T. Perez, “Autonomous sweet pepper harvesting for protected cropping systems,” IEEE Robotics and Automation Letters, vol. 2, no. 2, pp. 872-879, Apr., 2017.
[https://doi.org/10.1109/LRA.2017.2655622]
-
A. Silwal, J. R. Davidson, M. Karkee, C. Mo, Q. Zhang, and K. Lewis, “Design, integration, and field evaluation of a robotic apple harvester,” Journal of Field Robotics, vol. 34, no. 6, pp. 1140-1159, 2017.
[https://doi.org/10.1002/rob.21715]
-
Z. De-An, L. Jidong, J. Wei, Z. Ying, and C. Yu, “Design and control of an apple harvesting robot,” Biosystems Engineering, vol. 110, no. 2, pp. 112-122, Oct., 2011.
[https://doi.org/10.1016/j.biosystemseng.2011.07.005]
-
Y. Wang, Y. Yang, C. Yang, H. Zhao, G. Chen, Z. Zhang, S. Fu, M. Zhang, and H. Xu, “End-effector with a bite mode for harvesting citrus fruit in random stalk orientation environment,” Computers and Electronics in Agriculture, vol. 157, pp. 454-470, Feb., 2019.
[https://doi.org/10.1016/j.compag.2019.01.015]
- L. Mu, Y. Liu, Y. Cui, H. Liu, L. Chen, L. Fu, and Y. Gejima, “Design of end-effector for kiwifruit harvesting robot experiment,” 2017 ASABE Annual International Meeting, 2017.
-
Z. Yuanshen, L. Gong, C. Liu, and Y. Huang, “Dual-arm robot design and testing for harvesting tomato in greenhouse,” IFAC-Papers Online, vol. 49, no. 16, pp. 161-165, 2016.
[https://doi.org/10.1016/j.ifacol.2016.10.030]
-
Y.-C. Chiu, P.-Y. Yang, and S. Chen, “Development of the end-effector of a picking robot for greenhouse-grown tomatoes,” Applied Engineering in Agriculture, vol. 29, no. 6, pp. 1001-1009, 2013.
[https://doi.org/10.13031/aea.29.9913]
-
Q. Feng, W. Zou, P. Fan, C. Zhang, and X. Wang, “Design and test of robotics harvesting system for cherry tomato,” International Journal of Agricultural and Biological Engineering, vol. 11, no. 1, pp. 96-100, 2018.
[https://doi.org/10.25165/j.ijabe.20181101.2853]
-
N. Kondo, K. Yata, M. lida, T. Shiigi, M. Monta, M. Kurita, and H. Omori, “Development of an end-effector for a tomato cluster harvesting robot,” Engineering in Agriculture, Environment and Food, vol. 3, no. 1, pp. 20-24, 2010.
[https://doi.org/10.1016/S1881-8366(10)80007-2]
-
S. Hayashi, K. Shigematsu, S. Yamamoto, K. Kobayashi, Y. Kohno, J. Kamata, and M. Kurita, “Evaluation of a strawberryharvesting robot in a field test,” Biosystems Engineering, vol. 105, no. 2, pp. 160-171, Feb., 2010.
[https://doi.org/10.1016/j.biosystemseng.2009.09.011]
-
S. Hayashi, S. Yamamoto, S. Saito, Y. Ochiai, J. Kamata, M. Kurita, and K. Yamamoto, “Field operation of a movable strawberry-harvesting robot using a travel platform,” Japan Agricultural Research Quarterly: JARQ, vol. 48, no. 3, pp. 307-316, 2014.
[https://doi.org/10.6090/jarq.48.307]
-
K.-S. Han, S.-C. Kim, Y.-B. Lee, S.-C. Kim, D.-H. Im, H.-K. Choi, and H. Hwang, “Strawberry harvesting robot for bench -type cultivation,” Journal of Biosystems Engineering, vol. 37, no. 1, pp. 65-74, 2012.
[https://doi.org/10.5307/JBE.2012.37.1.065]
-
Y. Xiong, C. Peng, L. Grimstad, P. J. From, and V. Isler, “Development and field evaluation of a strawberry harvesting robot with a cable-driven gripper,” Computers and Electronics in Agriculture, vol. 157, pp. 392-402, Feb., 2019.
[https://doi.org/10.1016/j.compag.2019.01.009]
-
Y. Hui, H. Liu, H. Zhang, Y. Wu, Y. Li, Z. Fu, and D. Wang, “Design and Experiment of End-effector for Eggplant Picking Robot,” 2018 ASABE Annual International Meeting, 2018.
[https://doi.org/10.13031/aim.201800387]
-
S. Bachche and K. Oka, “Performance testing of thermal cutting systems for sweet pepper harvesting robot in greenhouse horticulture,” Journal of System Design and Dynamics, vol. 7, no. 1, pp. 36-51, 2013.
[https://doi.org/10.1299/jsdd.7.36]
-
C. W. Bac, J. Hemming, B.A.J. Van Tuijl, R. Barth, E. Wais, E. J. van Henten, “Performance evaluation of a harvesting robot for sweet pepper,” Journal of Field Robotics, vol. 34, no. 6, pp. 1123-1139, 2017.
[https://doi.org/10.1002/rob.21709]
-
E.J. Van Henten, B.V.J. Van Tuijl, J. Hemming, J. G, Kornet, J. Bontsema, and E. A. Van Osakai, “Field test of an autonomous cucumber picking robot,” Biosystems Engineering, vol. 86, no. 3, pp. 305-313, Nov., 2003.
[https://doi.org/10.1016/j.biosystemseng.2003.08.002]
-
J.N, Reed and R.D. Tillett, “Initial experiment in robotic mushroom harvesting,” Mechatronics, vol. 4, no. 3, pp. 265-279, Apr., 1994.
[https://doi.org/10.1016/0957-4158(94)90004-3]
-
J.N. Reed, S.J. Miles, J. Butler, M. Baldwin, and R. Noble, “AE-Automation and emerging technologies: Automatic mushroom harvester development,” Journal of Agricultural Engineering Research, vol. 78, no. 1, pp. 15-23, Jan., 2001.
[https://doi.org/10.1006/jaer.2000.0629]
-
S. Sakai, M. Iida, K. Osuka, and M. Umeda, “Design and control of a heavy material handling manipulator for agricultural robots,” Autonomous Robots, vol. 25, no. 3, pp. 189-204, 2008.
[https://doi.org/10.1007/s10514-008-9090-y]
-
A. Leu, M. Razavi, L. Langstädtler, D. Ristić-Durrant, H. Raffel, C. Schenck, A. Gräser, and B. Kuhfuss, “Robotic green asparagus selective harvesting,” IEEE/ASME Transactions on Mechatronics, vol. 22, no. 6, pp. 2401-2410, Dec., 2017.
[https://doi.org/10.1109/TMECH.2017.2735861]
- S. Cho, J. P. Jun, H. -Y. Jeong, and H. I. Son, “Design of a 4-Finger End-Effector for paprika harvesting,” 2018 18th International Conference on Control, Automation and System (ICCAS), Daegwallyeong, South Korea, pp. 255-257, 2018.
-
J. Shintake, V. Cacucciolo, D. Floreano, and H. Shea, “Soft robotic grippers,” Advanced Materials, vol 30, no. 29 pp. 1707035, 2018.
[https://doi.org/10.1002/adma.201707035]
-
C. J. Hohimer, H. Wang, S. Bhusal, J. Miller, C. Mo, and M. Karkee, “Design and field evaluation of a robotic apple harvesting system with a 3D-printed soft-robotic end-effector,” Transaction of the ASABE, vol. 62, no. 2, pp. 405-414, 2019.
[https://doi.org/10.13031/trans.12986]
- H. J, Jeong, S. W. Cho, and H. I. Son, “Development of soft gripper for automatic tomato harvesting robot in controlled environments horticulture,” KSAM Spring Conference, pp. 489-490, 2019.
-
H. Yaguchi, K. Nagahama, T. Hasegawa, and M. Inaba, “Development of an autonomous tomato harvesting robot with rotational plucking gripper,” 2016 IEEE/RSJ International Conference on Intelligent Robots and Systems (IROS), Deajeon, South Korea, pp. 652-657, 2016.
[https://doi.org/10.1109/IROS.2016.7759122]
-
J. Hemming, B.A.J. van Tuijl. W. Gauchel, and E. Wais, “Field test of different end-effectors for robotic harvesting of sweetpepper,” ISHS Acta Horticulture 1130, pp. 567-574, 2014.
[https://doi.org/10.17660/ActaHortic.2016.1130.85]
- J. Hemming, C. W. Bac, B.A.J. van Tuijl, R. Barth, J. Bontsema, E.J. Pekkeriet, and E. Van Henten, “A robot for harvesting sweet-pepper in greenhouses,” AgEng 2014, Zurich, Germany, 2014.
-
Y. Xiong, Y. Ge, L. Grimstad, and P. J. From, “An autonomous strawberry-harvesting robot: Design, development, integration, and field evaluation,” Journal of Field Robotics, vol. 37, no. 2, pp. 202-224, 2020.
[https://doi.org/10.1002/rob.21889]
-
H. Sarabu, K. Ahlin, and A. -P. Hu, “Graph-Based Cooperative Robot Path Planning in Agriculture Environments,” 2019 IEEE/ASME International Conference on Advanced Intelligent Mechatronics (AIM), Hong Kong, China, pp. 519-525, 2019.
[https://doi.org/10.1109/AIM.2019.8868747]
-
C. W. Bac, T. Roorda, R. Reshef, S. Berman, J. Hemming, and E. J. van Henten, “Analysis of a motion planning problem for sweet-pepper harvesting in a dense obstacle environment,”Biosystems Engineering, vol. 146, pp. 85-97, 2016.
[https://doi.org/10.1016/j.biosystemseng.2015.07.004]
-
H. J. Yoon, S. Y. Chung, and M. J. Hwang, “Shadow space modeling and task planning for collision-free cooperation of dual manipulators for planner task,” International Journal of Control, Automation and Systems, vol. 17, no. 4, pp. 995-1006, 2019.
[https://doi.org/10.1007/s12555-018-0236-1]
1998 부산대학교 생산기계공학과(공학사)
2000 부산대학교 지능기계공학과(공학석사)
2010 KAIST 기계공학과(공학박사)
2003~2005 LG전자 생산기술원 선임연구원
2005~2009 삼성 전자 ITD센터 책임연구원
2010 일본 동경대학교 생산기술연구소 박사후 연구원
2010~2012 독일 막스플랑크연구소 박사후연구원
2012~2015 삼성중공업 중앙연구소 수석연구원
2015~ 현재 전남대학교 지역·바이오시스템공학과 부교수
관심분야: field robotics, hybrid systems, haptics, teleoperation