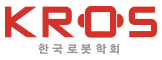
Prototype Parallel Gripper Mechanism Equipped with Assisting Grippers for Small Object Grasping and Experimental Validation
CopyrightⓒKROS
Abstract
The ability of the robot gripper to handle a wide range of objects significantly impacts its operational effectiveness. Among the robot grippers commonly used, the economically feasible choice is the relatively simple structure of a parallel gripper. To perform more densely packed tasks with a parallel gripper, it should be capable of handling small objects. Therefore, this study designs a parallel gripper mechanism equipped with assisting grippers to ensure smooth grasping of small objects. The parallel gripper is designed using a rack and pinion gear system, with two additional grippers on both side, and these assisting grippers are designed to be detachable. The two assisting grippers have different type of tip to grasp thin fabric shapes and thin stick shapes. The gripper prototype is used to verify the grasping capabilities for shapes achievable with a conventional parallel gripper and those intended for grasping with the assisting grippers through grasping experiments. Consequently, by equipping a conventional parallel gripper with assisting grippers as in this study, it becomes capable of handling a broader range of objects, in addition to its existing functionality.
Keywords:
Gripper, Grasping, Mechanical Design, Small Object Manipulation1. Introduction
Since the introduction of industrial robots, automation has been implemented in various fields[1,2]. Robots manipulators were introduced to replace human labor due to reasons such as working in hazardous environments and repetitive tasks[3]. Previously deployed robots performed tasks in separate spaces from humans, utilizing end-effector Tools tailored to the purpose of each robot[2,4,5]. Consequently, tools designed to perform specific functions have been developed.
The ongoing shift towards collaborative robots working alongside humans in shared spaces has increased the demand for versatile robotic functionalities[6]. The effectiveness of these robots, particularly in handling various tasks, relies heavily on the capabilities of their end-effector tools. Grippers, among the array of end-effector tools, play a pivotal role due to their proficiency in grasping objects[5]. This becomes even more crucial when these grippers are integrated into collaborative robot systems, emphasizing the necessity for efficient object manipulation. Given that many objects used by humans are small and thin, posing a challenge for conventional grasping, the gripper’s capacity to handle such objects becomes a key indicator of enhanced collaborative potential. Therefore, it is imperative for grippers to possess the versatility to grasp a diverse range of object types to meet the evolving needs of collaborative robots[7].
Various types of tools with different mechanisms have been developed, such as suction grippers, parallel grippers, and dexterous hands. Suction grippers are suitable for objects with flat surfaces[8,9] but struggle to grasp objects with contact surfaces smaller than a suction cup. Dexterous hands, on the other hand, offer advantages in grasping a variety of objects due to their high degrees of freedom[10]. However, they are challenging to control and have complex structures, making their application difficult[11]. Parallel grippers, in contrast, have simple structures and straightforward control[12]. Furthermore, they are easy to apply in various fields from an economic perspective[13].
Despite these advantages, it is challenging to grasp only one object in places where thin stick shapes such as bolts or pins are clustered due to the size of the parallel gripper. Additionally, when fabric-type thin shapes like paper or vinyl are intermingled between other objects, to selectively grasp only the thin shape, it is necessary not only to be able to grasp the thin shape but also to avoid touching other objects.
Therefore, this paper proposes a parallel gripper capable of versatile grasping. While the mechanisms of numerous parallel grippers have been studied extensively, the core objective of this research is to equip the gripper tips with additional assisting grippers with two kinds of the gripper tips to enhance their ability to grasp smaller objects. Therefore, the aim is to achieve grasping capabilities for thin-soft materials like film and tissue, as well as thin stick-shaped objects like hex key and bolt. In doing so, the parallel gripper is empowered with a higher grasping performance compared to conventional methods.
In the subsequent sections, research related to the parallel gripper is introduced. In Section 3, an overview of the mechanism of the parallel gripper used in this study is provided. Section 4 presents the grasping experiments and their results using the parallel gripper. Finally, in Section 5, the conclusion is presented.
2. Related Works
The parallel gripper is the most fundamental gripper widely utilized in industrial settings[13]. Parallel grippers primarily employ a pinching grasp. Generally, they are actuated using pneumatic or electric mechanisms. Electric grippers offer precision and ease of control, while pneumatic grippers provide high force capabilities[14]. Research has been ongoing to enhance the mechanism of conventional parallel grippers, modify their tips, and explore various other methods[15,16]. Furthermore, research has been conducted on using parallel grippers to grasp and employ separate tools[17-19].
Numerous studies have sought to enhance conventional grippers. However, grasping small and slippery objects like thin materials such as fabric-type thin materials such as vinyl and tissue, or stick shaped items like hex-key and bolt, remains challenging. While it is possible to grasp separate tools to handle these objects, economically, it is not an efficient approach to grasp a tool for each object. Moreover, the inclusion of a separate tool grasping task complicates the process of performing tasks swiftly.
Therefore, the gripper proposed in this study enhances grasping of small objects by adding assisting grippers with different tip shapes to the parallel gripper, resulting in improved grasping performance.
3. Gripper Mechanism Design
In this study, a gripper is introduced that enhances the grasping capabilities of conventional parallel grippers, enabling them to grasp objects they could already handle as well as previously challenging objects like vinyl, bolt, cables, and more. [Fig. 1(a)] illustrates the gripper with two additional assisting grippers alongside the typical configuration of a parallel gripper. These three grippers are designed through mechanisms commonly employed in conventional parallel grippers.
![[Fig. 1] [Fig. 1]](/xml/39605/JKROS_2024_v19n1_58_f001.jpg)
(a) Main structure of the gripper. (b) Main gripper mechanism in detail. (c) Assisting grippers mechanism in detail
The focus of proposed gripper is on stroke and functional implementation rather than gripping force. The stroke of the main gripper is set at 120mm, referencing the commercial gripper PHL-W 25 (Schunk). The assisting grippers are designed with a focus on grasping small objects. Given the thin nature of objects such as paper and vinyl, the gripper is structured to close completely when grasping these materials. To grasp small shapes like tiny wrenches and bolts, the gripper can open up to 9mm, and the tips are configured with varying shapes to accommodate the gripping of different objects, devising a mechanism for each object.
3.1 Main Gripper Mechanism
Parallel grippers are operated using various drive mechanisms, including pneumatic or electric. In particular, electric options offer flexibility with rack and pinion gears, linkage structures, linear actuators, and more. In this study, we employ the rack and pinion gear mechanism, one of the widely used mechanisms, to drive the parallel gripper[14]. [Fig. 1(b)] illustrates the structure of the parallel gripper. By coupling a servo motor with a pinion gear and meshing the rack gear, which can move along a guide, a parallel motion is achieved.
[Fig. 2] illustrates the concept of the main gripper, which is driven by a rack and pinion system. The gripper composed of a rack and pinion can be controlled based on the movement of the pinion gear, where the distance between the fingers due to the motion of the pinion gear can be regulated. Let da denote the distance from the center of the pinion to the contact surface of the finger. If the motor rotates by an angle θp, the distance between the finger and the contact surface is denoted as db.
(1) |
In this context, zp represents the number of teeth on the pinion gear, and pr is the pitch of the rack gear. Through the above expression, it is possible to control the position of the fingers based on the rotation angle of the motor.
3.2 Assisting Grippers Mechanism
Two assisting grippers are mounted on each side of the parallel gripper. [Fig. 1(c)] illustrates the structure of the assisting grippers. The gripper has one tip fixed, while the other tip performs grasping by translating. The translating tip is capable of linear motion through guides, and this movement is facilitated by two links connected to servo motor. Both assisting grippers share the same mechanism but have different tip configurations based on the shape of the objects they are intended to grasp. The tips designed for grasping fabric-type thin materials are rounded at the end to pull and hold the target object. The tips for grasping thin stick-shaped objects like bolt and hex key have a diagonal shape to slide into beneath the target object for a secure hold.
[Fig. 3] depicts the concept of the assisting grippers, driven through a slider-crank mechanism. The fingers are actuated using this mechanism, while the opposite finger remains stationary. The assisting grippers can be controlled based on the rotation angle of motor 1, determining the movement of the links and the displacement of the fingers. Initally, let l1 and l2 represent the length of link 1 and 2, and ds the distance between the contact surface of the moving finger and the connection point. The angle between link 1 and the moving finger at the initial position is denoted as θo, and the distance from the motor 1 connection axis on link 1 to the joint connecting link 2 and the moving finger is denoted as h. Therefore, the angle l1 formed between link 2 and the moving finger can be determined.
(2) |
(3) |
If the initial distance between the moved finger and the fixed finger is denoted as do,
(4) |
When motor 1 rotates by an angle θm to grasp an object at the initial position, let θg represent the angle between link 1 and the moved finger. The angle θ2 formed between link 2 and the moved finger can be defined.
(5) |
(6) |
(7) |
Therefore, when motor 1 rotates by and angle θm, the distance between the fixed finger and the moved finger denoted as dg is given as follows.
(8) |
By utilizing the above equation, it is possible to control the position of the finger based on the rotation angle of the motor. For motor 2, its role is to rotate the entire grasping component connected to motor 1. Depending on the initial configuration, it is rotated to a position perpendicular to the ground.
3.3 Operation of the Gripper
When grasping objects that can be handled by the conventional parallel gripper, the main parallel gripper is used for grasping, and in this case, it operates with the assisting grippers positioned backward, as depicted in [Fig. 4(a)]. The assisting grippers, upon moving backward, approaches the object to be grasped and executes the grasping action as depicted in [Fig. 4(b)].
![[Fig. 4] [Fig. 4]](/xml/39605/JKROS_2024_v19n1_58_f004.jpg)
(a) In the case of using main gripper, the assisting gripper retracts to the back ward. (b) Grasping action of main gripper. (c) In the case of using assisting grippers, only the designated assisting gripper moves forward. (d) Grasping action of assisting grippers
When grasping fabric-type thin materials and thin stick-shape objects, the corresponding assisting grippers are positioned forward, as shown in [Fig. 4(c)]. After moving forward, the assisting gripper approaches the object to be grasped and performs the grasping action, as illustrated in [Fig. 4(d)].
4. Experiment
In this section, the prototype of the gripper introduced in the Section 3 is fabricated using a 3D printer, and grasping experiments are conducted to evaluate its capabilities. Separate grasping experiments are performed for both the main parallel gripper and the assisting grippers. The gripper is installed on installed on the manipulator (UR5e, Universal Robot) for operation. Additionally, the experiments assume prior knowledge of the object’s location. Also, the experimental videos can be viewed in the [supplemental experiment video] in Appendix section.
4.1 Grasping Experiment of main Gripper
Experiments were conducted to verify the grasping performance of the main gripper’s conventional parallel gripper. To assess the gripper’s grasping performance, grasping experiments are carried out on 3D printed objects with typical shapes, including a rectangular cuboid, a cylinder, and a spherical object.
[Fig. 5(a)] illustrates the grasping procedure for the main gripper experiments. To perform the grasping action with the main gripper, the assisting grippers had been retracted to the rear prior to grasping and then the grasping operation was executed. [Fig. 5(b)] confirms the stable grasping of the three target objects through the operational process depicted in [Fig. 5(a)].
4.2 Grasping Experiment of Assisting Grippers
The assisting grippers are responsible for grasping different target with experiments conducted for grasping both the center and the edge of each material. The second experiment utilizes a different assisting grippers compared to the first experiment to grasp thin stick-shaped objects. The target objects for this experiment include 20 AWG cable, M2 hex socket head cap screw, M2.5 socket set screw, and M1.6 hex key. [Fig. 6] illustrates the operational procedures using the assisting grippers. [Fig. 6(a)] demonstrates the process of pulling and grasping the center of vinyl. [Fig. 6(b)] shows the procedure for pulling and grasping the edge of the same materials. [Fig. 6(c)] displays the process of digging into and grasping slender rod- shaped materials. Additionally, the assisting gripper moves forward only when the respective assisting grippers are employed for grasping.
![[Fig. 6] [Fig. 6]](/xml/39605/JKROS_2024_v19n1_58_f006.jpg)
(a) Grasping process of assisting gripper for vinyl to grasp the center of vinyl. (b) Grasping process of assisting gripper for vinyl to grasp the edge of vinyl. (c) Grasping process of assisting gripper for hex key
[Fig. 7(a)] displays the experimental results of grasping vinyl and tissue around the center and edge, while [Fig. 7(b)] shows the results of grasping cable, bolt, set screw, and hex key. This confirms the capability of each assisting gripper to grasp objects according to their intended purpose.
5. Conclusion
This study improved upon the limitations of traditional parallel grippers by incorporating assisting grippers. This enhancement not only facilitates the efficient handling of small objects but also preserves standard grasping capabilities, resulting in improved performance. These findings have the potential to broaden the scope of tasks that parallel grippers can undertake.
In addition, the study experimented with two prototype assisting grippers that did not have specific materials or tip characteristics. In the future, assisting grippers designed for handling thin, fabric-like materials will use high-friction materials for its tips to handle slippery materials like paper, depending on the object’s characteristics. This approach allows for a wider range of object handling compared to what was studied here.
References
-
J. F. Bard, “An assessment of industrial robots: Capabilities, economics, and impacts,” Journal of operations Management, vol. 6, no. 2, pp. 99-124, Feb., 1986.
[https://doi.org/10.1016/0272-6963(86)90020-3]
- J. Fryman and B. Matthias, “Safety of industrial robots: From conventional to collaborative applications,” ROBOTIK 2012; 7th German Conference on Robotics, Munich, Germany, pp. 1-5, 2012, [Online], https://ieeexplore.ieee.org/document/6309480/metrics#metricst, .
-
K. Jung, B. Chu, and D. Hong, “Robot-based construction automation: An application to steel beam assembly (Part II),” Automation in Construction, vol. 32, pp. 62-79, Jul., 2013.
[https://doi.org/10.1016/j.autcon.2012.12.011]
- H. A. Yanco and J. L. Drury, “A taxonomy for human-robot interaction,” the AAAI fall symposium on human-robot interaction, pp. 111-119, 2002, [Online], https://www.researchgate.net/publication/228550993_A_Taxonomy_for_Human-Robot_Interaction, .
-
P. V. P. Reddy and V. Suresh, “A review on importance of universal gripper in industrial robot applications,” Int. J. Mech. Eng. Robot. Res, vol. 2, no. 2, pp. 255-264, Apr., 2013.
[https://doi.org/10.18178/ijmerr]
-
C. Vogel, C. Walter and N. Elkmann, “Safeguarding and supporting future human-robot cooperative manufacturing processes by a projection-and camera-based technology,” Procedia Manufacturing, vol. 11, pp. 39-46, 2017.
[https://doi.org/10.1016/j.promfg.2017.07.127]
-
A. Dameitry and H. Tsukagoshi, “Lightweight pneumatic semi-universal hand with two fingers aimed for a wide range of grasping,” Advanced Robotics, vol. 31, no. 23-24, pp. 1253-1266, Oct., 2017.
[https://doi.org/10.1080/01691864.2017.1392346]
-
A. Koivikko, D.-M. Drotlef, C. B. Dayan, V. Sariola, and M. Sitti, “3D‐Printed Pneumatically Controlled Soft Suction Cups for Gripping Fragile, Small, and Rough Objects,” Advanced Intelligent Systems, vol. 3, no. 9, Sept., 2021.
[https://doi.org/10.1002/aisy.202100034]
-
Y. Sim and S. Jin, “Gripper Design with Adjustable Working Area for Depalletizing Delivery Cardboard box of Various Sizes,” Journal of Korea Robotics Society, vol. 18, no. 1, pp. 29-36, Feb., 2023.
[https://doi.org/10.7746/jkros.2023.18.1.029]
-
H.-S. Yu, M.-C. Kim, and J.-B. Song, “Tendon-driven Adaptive Robot Hand,” Journal of Korea Robotics Society, vol. 9, no. 4, pp. 258-263, Nov., 2014.
[https://doi.org/10.7746/jkros.2014.9.4.258]
-
OpenAI, M. Andrychowicz, B. Baker, M. Chociej, R. Jozefowicz, B. McGrew, J. Pachocki, A. Petron, M. Plappert, G. Powell, A. Ray, J. Schneider, S. Sidor, J. Tobin, P. Welinder, L. Weng, and W. Zaremba, “Learning dexterous in-hand manipulation,” The International Journal of Robotics Research, vol. 39, no. 1, pp. 3-20, Nov., 2019.
[https://doi.org/10.1177/0278364919887447]
-
J. Tanaka, D. Yamamoto, H. Ogawa, H. Ohtsu, K. Kamata, and K. Nara, “Portable compact suction pad unit for parallel grippers,” Advanced Robotics, vol. 34, no. 3-4, pp. 202-218, 2020.
[https://doi.org/10.1080/01691864.2019.1686421]
-
Z. Samadikhoshkho, K. Zareinia, and F. Janabi-Sharifi, “A brief review on robotic grippers classifications,” 2019 IEEE Canadian Conference of Electrical and Computer Engineering (CCECE), Edmonton, Canada, pp. 1-4, 2019.
[https://doi.org/10.1109/CCECE.2019.8861780]
-
B. Zhang, Y. Xie, J. Zhou, K. Wang, and Z. Zhang, “State-of-the-art robotic grippers, grasping and control strategies, as well as their applications in agricultural robots: A review,” Computers and Electronics in Agriculture, vol. 177, Oct., 2020.
[https://doi.org/10.1016/j.compag.2020.105694]
-
Y. Tsugami, T. Barbié, K. Tadakuma, and T. Nishida, “Development of universal parallel gripper using reformed magnetorheological fluid,” 2017 11th Asian control conference (ASCC), Gold Coast, QLD, Australia, pp. 778-783, 2017.
[https://doi.org/10.1109/ASCC.2017.8287269]
-
L. Yifan, X. Zhijie, W. Jian, Y. Honghao, W. Miao, and L. Yiwei, “A novel design of a parallel gripper actuated by a large-stroke shape memory alloy actuator,” International Journal of Mechanical Sciences, vol. 159, pp. 74-80, Aug., 2019.
[https://doi.org/10.1016/j.ijmecsci.2019.05.041]
-
N. Nahum and A. Sintov, “Robotic manipulation of thin objects within off-the-shelf parallel grippers with a vibration finger,” Mechanism and Machine Theory, vol. 177, Nov., 2022.
[https://doi.org/10.1016/j.mechmachtheory.2022.105032]
-
Z. Hu, W. Wan, K. Koyama, and K. Harada, “A mechanical screwing tool for parallel grippers—Design, optimization, and manipulation policies,” IEEE Transactions on Robotics, vol. 38, no. 2, pp. 1139-1159, Apr., 2021.
[https://doi.org/10.1109/TRO.2021.3091282]
-
Z. Hu, W. Wan, and K. Harada, “Designing a mechanical tool for robots with two-finger parallel grippers,” IEEE Robotics and Automation Letters, vol. 4, no. 3, pp. 2981-2988, Jul., 2019.
[https://doi.org/10.1109/LRA.2019.2924129]
Appendix
Appendix
Experimental videos can be viewed in the address below: [https://youtu.be/Yk0ZNJH2NH8].
2020 한양대학교 ERICA 로봇공학과(학사)
2022~현재 한양대학교 융합로봇시스템학과 석박사통합과정
관심분야: Gripper, Grasping, Robot mechanism design, Art and entertainment robot, and their applications
2023 한양대학교 ERICA 로봇공학과(학사)
2023~현재 한양대학교 융합로봇시스템학과 석사과정
관심분야: Robot manipulator control, Gripper, Grasping, Autonomous mobile robot
2023 한양대학교 ERICA 로봇공학과(학사)
2023~현재 한양대학교 융합로봇시스템학과 석사과정
관심분야: Robot manipulator control, Autonomous mobile robot, Grasping
1997 홍익대학교 기계공학과(학사)
2002 홍익대학교 기계공학과(석사)
2013 한양대학교 메카트로닉스학과(박사)
2013~현재 한양대학교 조교수
관심분야: Robot manipulator control, Robot mechanism design, Autonomous mobile robot, Construction robot, Computer vision, and their applications