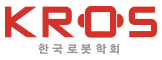
단일 펌프를 이용하여 공압 그리퍼와 진공 그리퍼의 동시 구현이 가능한 그리핑 시스템의 개발
CopyrightⓒKROS
Abstract
In recent years, the use of robot arms has increased rapidly in both industrial and service applications. Unlike production sites, where only one type of gripper is used for productivity, service sites often use a tool changer to replace fingered grippers or vacuum grippers to cover various objects to be grasped. To this end, a tool changer-based pneumatic grasping system was developed in this study. In order to simultaneously use a positive pressure-based pneumatic gripper and a negative pressure-based vacuum gripper, a small vane pump capable of generating positive and negative pressures depending on the direction of rotation was developed. Experiments with actual prototypes have shown that the pneumatic system based on the developed vane pump can effectively realize both pneumatic grippers and vacuum grippers.
Keywords:
Pneumatic Gripping System, Pump Module, Tool Changing System1. 서 론
최근 로봇 기술의 발전과 고임금 및 구인난 등의 사회적 요구로 인하여 다양한 분야에서 로봇의 활용이 점차 보편화되고 있다. 부품 조립 및 물품 운송과 같은 단순 반복 작업을 수행하는 기존의 산업용 로봇에서 요리와 서빙 및 의료 등 복잡한 작업을 수행하기 위한 서비스 로봇까지 로봇의 필요성 및 수요가 증가하고 있으며, 이러한 작업 수행에 적합한 엔드 이펙터(end-effector)에 대한 관심 또한 높아지고 있다[1,2].
기존의 산업 현장에서는 여러 대의 로봇으로 조립과 물품 운송을 위한 대상물 파지를 위해 공장 전체에 대형 펌프 등을 활용한 공압 시스템을 구축하여 그리퍼를 사용하여 효율적으로 작업을 수행할 수 있었다. 그러나 서비스 현장에서는 공압으로 인한 소음과 공간상의 제한으로 인하여 공압 시스템의 구축이 어려우며, 다양한 작업을 수행하기 위해서 단일 그리퍼가 아닌 여러 종류의 그리퍼를 교체하면서 사용하는 것이 필요하지만, 그리퍼의 높은 비용으로 인해 사용자의 부담이 증가하게 된다.
최근 다양한 형태의 공압 그리퍼가 개발되고 있다[3]. 일부 공압 그리퍼는 음식물과 같이 가볍고 형태를 유지해야 하는 물체를 고무 또는 실리콘으로 제작한 그리퍼 팁에 압축 공기를 인가하여 물체를 파지하고, 비닐 등으로 포장된 음식물의 경우는 진공을 이용하여 물체를 흡착하여 파지한다. 그러나 최대 가반하중이 1 kg 미만이므로 가벼운 물체만 다룰 수 있다는 점과 작업 물체에 따라 압축공기를 제공할 압축기와 진공을 제공할 펌프가 필요하여 시스템 비용의 증가와 불편함이 수반된다는 단점이 있다. 따라서 로봇 말단에서 툴 교환이 용이하며, 1 kg 이상 물체를 파지할 수 있는 공압 파지 시스템이 필요하다. 또한, 공간상의 제약을 받지 않아야 한다.
본 연구에서는 [Fig. 1]와 같이 다양한 공압 그리퍼 교체 및 사용이 가능하며, 소규모로 구축 가능한 펌프 모듈을 제작하여 최대 가반하중이 2 kg까지 가능한 공압 그리핑 시스템을 개발하였다.
[Fig. 1]의 펌프 모듈을 통해 공기 압축기 또는 공압 라인을 갖출 수 없는 상황에서 작업 수행에 필요한 공압 기반 그리퍼를 사용할 수 있도록 하여, 사용자는 산업현장뿐만 아니라 식당 등의 서비스 현장에서도 로봇과 공압을 활용한 작업을 수행할 수 있다.
본 논문은 다음과 같이 구성한다. 2장에서는 툴 체인저기능이 있는 펌프 모듈의 구조와 원리에 대해 설명하고, 3장에서는 펌프 모듈 기반의 공압 그리핑 시스템에 대해 설명한다. 4장에서는 공압 그리핑 시스템의 실험적 검증을 수행하고 5장에서 결론으로 마무리한다.
2. 펌프 모듈의 구조 및 원리
2.1 펌프 모듈의 구조
[Fig. 2(a)]와 같이 동력 전달 기능을 포함한 툴 체인저는 로봇의 말단부에 부착되는 마스터와 툴에 부착되는 슬레이브로 구성되어 있는데, 이때 마스터에 모터가 내장되어 모터의 동력을 자석 커플링을 통해 슬레이브 및 궁극적으로 툴에 전달하는 구조로 설계되어 있다. 종래의 툴 체인저는 툴의 교체에만 관여하였지만, [Fig. 2(b)]의 제안된 툴 체인저에서는 툴 교체 외에도 동력원의 역할도 수행하므로 툴 체인저에 장착되는 툴의 경우 별도의 동력원을 가질 필요 없이 기구부만으로 구성될 수 있다.
이때 마스터에서 전달받은 회전 동력을 툴에 내장된 펌프의 입력으로 사용하면 펌프의 구동을 통해서 필요한 공압을 생성할 수 있다. 이렇게 생성된 공압 시스템은 기존의 산업 현장에서 사용되는 펌프와 달리 별도의 공압 밸브 없이도 모터의 회전속도 조절을 통하여 유량 및 공압의 조절이 가능하다. 즉, 기존의 공압 시스템은 펌프와 밸브를 별도로 제어하여 유체의 유량과 압력을 조절하는 반면에, 제안된 공압 시스템은 펌프와 밸브를 통합하여 하나의 모터로 회전속도를 조절함으로써 유량과 압력을 조절할 수 있어 시스템이 보다 단순해지고 조절이 용이하게 된다. 또한, [Fig. 2(b)]에서 보듯이, 모터를 통해 공압을 조절할 수 있으므로 다양한 사양을 가진 그리퍼들을 하나의 동력원으로 구동할 수 있다. 이러한 기능 덕분에 여러 종류의 툴을 교체하면서 작업을 수행할 수 있어서 전체 시스템 비용을 절감할 수 있다.
2.2 펌프 모듈의 원리
제안한 툴 체인저 시스템은 모터에서 전달받은 회전력에 기반하여 펌프 모듈에서 공압 또는 진공을 생성할 수 있다. 그러므로 공압을 이용한 2지 그리퍼 또는 소프트 그리퍼 외에도, 진공을 이용한 진공 그리퍼를 구동할 수 있다. 이를 위해서 공압을 위한 양압(또는 정압) 및 진공을 위한 음압(또는 부압)의 생성이 가능한 회전식 베인 펌프(rotary vane pump)의 구조를 활용하여 펌프 모듈을 설계하였다.
회전식 베인 펌프의 가장 일반적인 유형은 [Fig. 3]과 같다. 회전식 베인 펌프는 회전자, 고정자, 베인(vane) 등으로 구성되어 있고, 회전자와 고정자 사이에 작은 공간이 형성되도록 두 파트의 중심이 편심 되어 있다. 회전자 내부에는 베인이 삽입되는 슬롯이 있고, 회전자가 회전함에 따라 원심력에 의해 베인은 바깥쪽으로 이동하여 고정자의 내면과 접촉을 지속적으로 유지하며 회전한다.
[Fig. 3]에서 보듯이, 고정자와 베인, 그리고 편심 되어 위치한 회전자로 인하여 두 베인 사이에 초승달 모양의 챔버가 형성되고 대기압과 연결된 입구 포트 A를 통해 챔버 내부에 유체가 유입된다. 베인이 회전자와 함께 회전함에 따라 챔버의 형상이 변형되면서 내부의 유체를 압축시키고, 베인(B)이 출구 포트 C에 도달하면 압축되었던 유체가 외부로 배출되면서 유량 및 공압이 생성된다[4].
2.3 펌프 모듈의 사양 선정
펌프 모듈의 설계에 앞서서 펌프의 성능지표 중 하나인 유량을 계산하기 위해서는 펌프의 기하학적 구조와 유량 사이의 관계를 알아야 한다. [Fig. 4]와 같이 회전자의 중심이 고정자의 중심보다 위에 있는 형태의 펌프 유량 Q는 다음과 같다[5].
(1) |
여기서 Ds은 고정자의 직경, Dr은 회전자의 직경, L은 회전자 및 베인의 길이, N은 펌프의 회전속도이다. 식 (1)에서 은 챔버의 부피에 해당하므로, 펌프 유량은 내부에 생성되는 챔버의 부피 및 펌프의 회전속도에 비례하여 유량이 증가한다.
한편, 그리퍼의 파지력(gripping force)은 압력에 의해서 결정되므로, 펌프의 사양에 있어서 압력도 중요한 항목이다. 펌프의 압력을 계산하기 위해서 기계적 에너지 방정식 및 확장 베르누이(extended Bernoulli) 방정식을 활용하여 다음과 같은 에너지 식을 구할 수 있다[6].
(2) |
여기서 γ는 유체의 비중량, hs는 회전축이 회전하며 발생하는 에너지 손실을 나타내는 축일 수두(shaft work head), hL = loss/g은 유체가 흘러가면서 발생하는 에너지 손실을 의미하는 수두 손실(head loss), g는 중력가속도이다. 이때, loss는 유동할 때 마찰에 의해 발생하는 유용 에너지 또는 가용 에너지 손실이다.
유량 연속방정식 Q = AinVin = AoutVout에서 [Fig. 4]와 같이 펌프의 입구 단면적(Ain)와 출구 단면적(Aout)의 차이가 매우 작으므로 속도의 차이 또한 작다. 그리고 펌프의 입구 높이(zin)와 출구 높이(zout)의 차이가 거의 없으므로, 식 (2)는 다음과 같이 단순하게 나타낼 수 있다.
(3) |
여기서 ha을 실제 수두 상승이며, 입구와 출구 사이의 압력 차이에 비례하게 된다.
펌프의 성능은 적정 유량 및 압력을 통해 결정되는데, [Fig. 5]와 같은 성능 곡선 그래프에서 펌프의 성능과 유량의 관계를 알 수 있다. 유량이 커질수록 수두는 낮아지고, 효율은 표준 또는 설계 유량까지는 증가한다. 이때, 실제 수두 상승(ha)은 압력에 비례하므로, 결과적으로 유량과 압력이 반비례 관계임을 알 수 있다.
또한, [Fig. 5]의 펌프 시스템 곡선은 식 (4)와 같은 시스템 방정식으로 나타낼 수 있다.
(4) |
여기서 K는 시스템 내에 발생하는 모든 손실을 반영하는 상수이다. 위 식은 펌프로부터 얻어지는 유체의 실제 수두와 유량과의 관계를 보여준다. [Fig. 5]에서 펌프 곡선과시스템 곡선의 교점을 동작점(duty point)이라 하는데, 이 점은 시스템 방정식과 펌프 방정식을 모두 만족시키는 수두와 유량을 나타내어 실제로 펌프가 작동하는 상태를 표시하는 점이다. 작동점이 펌프의 최고 효율점 근처에 있는 것이 이상적이므로 펌프 사양의 선정에 있어서 적절한 효율을 내기 위해서는 적정한 유량 및 압력의 선정이 필요하다.
3. 툴 체인징 기반의 펌프 모듈 설계
3.1 툴 체인징 기반의 펌프 모듈 구조 설계
앞서 2.1절에서 설명한 바와 같이, 로봇에 장착된 툴 체인저의 마스터로부터 툴에 장착된 슬레이브로 동력을 전달하기 위해 [Fig. 6]와 같이 자석 커플링을 이용하여 회전력을 전달한다. 이때, 회전력을 전달받는 슬레이브의 자석 커플링은 축과 연결되어 펌프 모듈 내부의 회전자를 회전시켜서 펌프를 구동하게 된다.
3.2 펌프 모듈의 유동 해석
펌프 모듈의 제작에 앞서 2.3절에서 언급한 고정자의 직경, 회전자의 직경, 회전자 및 베인의 길이 등과 같은 설계 변수에 따라 펌프가 생성 가능한 압력과 유량 등의 성능 변화 및 최대 0.3 bar의 압력 생성 가능성을 확인하기 위해 3D CAD 모델을 활용한 전산유체역학(CFD) 해석을 수행하였다. 설계 모델을 통해 시뮬레이션을 진행하기 위해서는 [Fig. 7]와 같이 회전자의 속도와 특정 지점에 경계조건을 설정하여야 한다. [Fig. 7]와 같이 회전자의 회전 방향을 설정한다면, 펌프의 입구는 대기압에 노출되어 있고, 출구는 그리퍼에 연결되며, 베인이 접촉하며 회전하는 면은 고정자로 설정할 수 있다.
이처럼 펌프 모듈의 구조 설계 이후 CFD 해석을 통하여 공압이 생성 및 설계 변수의 변화에 따른 유량 및 압력의 변화 등을 알 수 있다.
4. 펌프 모듈의 성능 검증
4.1 펌프 모듈 구동 및 성능 검증
위에서 제작된 펌프 모듈을 구동하면 회전 방향에 따라서 양압 및 음압이 생성되어 공압 그리퍼와 진공 그리퍼를 구동할 수 있다. 3.2절에서 수행한 해석 결과와 같이 공압 및 유량이 생성되는지를 검증하기 위해 [Fig. 9]와 같이 펌프의 출구부에 압력센서와 유량센서를 연결하여 압력과 유량을 측정하는 실험을 수행하였다.
펌프의 유량은 식 (1)과 같이 모터의 회전속도에 비례하므로, 본 실험에서는 모터의 회전속도를 변화시키면서 압력 및 유량을 측정하였다. 모터의 회전속도를 500 rpm씩 가속시켜서 4500 rpm에 도달한 후에 0 rpm까지 감속하면서 유량을 측정하였으며, 이를 식 (1)에서 계산한 값과 함께 [Fig. 10]에 나타내었다. 계산 값 및 측정값 모두 회전속도에 비례하여 증감하였지만, 2000 rpm 이상에서는 펌프의 유량이 측정값과 계산 값 사이에 큰 차이가 발생하였는데, 이는 회전속도가 증가할수록 고정자 내부와 접촉하며 회전하는 베인 표면과 내부 사이의 마찰손실이 증가하여 펌프의 효율이 감소하기 때문인데, 이는 시뮬레이션에서 이러한 마찰을 고려하지 않은 결과이다.
보다 정확한 시뮬레이션을 위해서는 이러한 마찰 현상을 정확하게 반영하여야 한다. 그러나 본 연구에서는 새로운 개념의 펌프 개발이 아니라, 잘 알려진 베인 펌프를 개발 대상인 그리핑 시스템의 크기와 목적에 부합하도록 개량 설계하는 것이 목적이므로, 펌프 내에서의 마찰 현상과 같은 고도의 유체역학적인 해석은 배제하였다.
펌프의 압력 측정은 유량 측정과 동일한 방식으로 진행하였는데, [Fig. 11]에 측정한 압력을 대기압과의 차이로 나타내었다. 최고 속도인 4500 rpm에서 최대 압력인 약 0.17 bar가 측정되었는데, 이는 3.3절에서 진행한 CFD 해석에서의 1.25 bar의 대략 70%에 해당한다.
4.2 공압 그리핑 시스템 적용성 검증
3.1절에서 설계된 툴 체인저 기반의 펌프 모듈 및 공압 기반의 그리퍼를 이용하여 툴 체인징을 포함한 그리퍼의 작동 및 작업 수행 능력을 검증하기 위한 실험을 수행하였다.
먼저 다양한 재질 및 무게를 대상으로 진공을 이용한물체 파지 실험을 [Fig. 12]와 같이 진행하였다. 그림에서 보듯이, 플라스틱, 알루미늄, 나무 등 다양한 재질의 물체를 최대 2 kg까지 파지 가능함을 알 수 있다.
제작된 베인 펌프에서 생성한 진공을 사용하여 진공 그리퍼의 단일 흡착 패드에 발생하는 흡입력은 다음과 같다.
(5) |
여기서 W는 흡입력, C는 흡착패드의 면적, P는 압력, f는 안전율이다. 이때, 흡입 방향이 수직일 때는 0.25 이상, 수평일 때는 0.125 이상의 값을 적용한다. [Fig. 13]에서 진행한 실험의 경우 수직 방향으로 물체를 들어올렸으며, 최소한의 안전율을 적용하였을 때 물체를 안정적으로 파지 할 수 있는 상황을 고려하기 위해 f = 0.25로 적용하였다. 이때의 예상 흡입력은 4.71 N이고, 해당 실험에 사용한 흡착패드의 개수가 4개이므로 식 (5)을 통한 예상 흡입력과 실험을 통해 측정한 실제 흡입력이 거의 일치함을 알 수 있다.
이번에는 베인 펌프에서 생성한 양압을 공압 그리퍼에 공급할 때 발생하는 파지력을 측정하는 실험을 [Fig. 13]과 같이 수행하였다.
실험에 사용한 공압 그리퍼는 [Fig. 13]와 같이 파지 물체의 종류에 따라 다른데, 파지 물체의 질량에 따라 필요한 힘은 다음과 같다.
(6) |
여기서 m은 파지 물체의 질량, g는 중력가속도, a는 안전율이다. [Fig. 13]과 식 (6)에서 a= 4로 적용하여 종합하면, 사용된 베인 펌프에 기반한 공압 그리퍼의 가반하중은 약 1 kg임을 알 수 있다.
앞서 언급하였듯이, 진공 그리퍼를 사용하여 플라스틱 도마, 알루미늄 분동, 나무 판자를 대상으로 100회 파지 반복 실험을 수행하였으며, 공압 2지 그리퍼 및 소프트 그리퍼를 사용하여 플라스틱 원기둥과 금속 재질의 연필통을 대상으로 100회 파지 반복 실험을 수행하였다. 펌프 모듈의 안정적인 공압 및 유량 공급에 따른 파지 안정성을 확인하기 위해서, 시작 지점에서 물체를 파지한 후에 목표 지점에 물체를 놓는 작업을 로봇의 정격 속도로 반복 진행하였다. 이러한 실험의 결과, 세 종류의 그리퍼 모두 실험을 수행하는 동안 물체를 안정적으로 파지하였고, 100회 중 진공 그리퍼는 95회, 공압 2지 그리퍼와 소프트 그리퍼는 91회 성공하였다. 이를 통해 본 연구에서 제안한 툴 체인징 기반의 공압 그리핑 시스템이 높은 성공률로 작동함을 확인하였다.
5. 결 론
본 연구에서는 단일의 베인 펌프 모듈을 활용하여, 양압에 기반한 공압 그리퍼와 음압에 기반한 진공 그리퍼를 하나의 시스템으로 구현한 새로운 개념의 공압 그리핑 시스템을 개발하였다. 제작한 펌프 모듈은 별도의 모터 없이 툴 체인저로부터 동력을 전달받아 구동하며, 최대 12.5 L/min의 유량과 최대 1.17 bar의 압력을 그리퍼로 공급할 수 있다. 펌프 모듈을 통해 생성된 공압을 공급하여 2지 그리퍼, 진공 그리퍼 및 소프트 그리퍼를 구동하여 다양한 형상의 물체를 안정적으로 파지 및 작업이 가능함을 확인하였다. 제안된 툴 체인징 기반의 공압 그리핑 시스템은 종래의 단순 반복작업이 필요한 산업 현장 외에도 툴의 교체를 통한 다양한 작업이 필요한 서비스 현장까지 여러 분야에서 활용 가능하다.
본 연구에서 사용한 물체보다 더 큰 물체를 다루거나 빠른 집기-놓기 작업을 수행하기 위해서는, 가속기 등을 활용하여 펌프의 회전 속도를 높이거나 마찰로 인해 발생하는 손실을 최소화할 수 있는 재질로 제작하는 것이 바람직하다.
Acknowledgments
This research was supported by the MOTIE under the Industrial Foundation Technology Development Program supervised by the KEIT (No. 20015198)
References
-
J. E. Bobrow and B. W. McDonell, “Modeling, identification, and control of a pneumatically actuated, force controllable robot,” IEEE Transactions on Robotics and Automation, vol. 14, no. 5, pp. 732-742, Oct., 1998.
[https://doi.org/10.1109/70.720349]
-
R. Mykhailyshyn, V. Savkiv, P. Maruschak, and J. Xiao, “A systematic review on pneumatic gripping devices for industrial robotst,” Transport, vol. 37, no. 3, pp. 201-231, Aug., 2022.
[https://doi.org/10.3846/transport.2022.17110]
-
Z. Wang, K. Or, and S. Hirai, “A dual-mode soft gripper for food packaging,” Robot and Autonomous System, vol. 125, 103427, Mar., 2020.
[https://doi.org/10.1016/j.robot.2020.103427]
-
B. S. Ramprasad and T. S. Radha, “On some design aspects of rotary vane pumps,” Vacuum, vol. 23, no. 7, pp. 245-249, Jul., 1973.
[https://doi.org/10.1016/0042-207x(73)90071-7]
-
A. Mohammed, M. Nabil, E. Ahmed, and M. H. Ashraf, “Flow modeling and performance assessment of rotary sliding vane pump using computational fluid dynamics,” IEEE Transactions on Mechatronics Journal of Al Azhar University Engineering Sector, vol. 13, no. 49, pp. 1268-1288, Nov., 2018.
[https://doi.org/10.21608/AUEJ.2018.18942]
- B. R. Munson, T. H. Okiishi, W. W. Huebsch, and A. P. Rothmayer, 2013, Jan., 13th, Fluid Mechanics (7th) [Online], http://students.aiu.edu/submissions/profiles/resources/onlineBook/L5g8S6_Fundamentals_of_Fluid_Mechanics-_7.pdf, ., Accessed: Aug. 16, 2022.
2020 세종대학교 기계공학과(학사)
2020~현재 고려대학교 메카트로닉스학과(석사과정)
관심분야: 그리퍼 설계, 로봇 파지
1983 서울대학교 기계공학과(공학사)
1985 서울대학교 기계공학과(공학석사)
1992 MIT 기계공학과(공학박사)
1993~현재 고려대학교 기계공학부 교수
관심분야: 로봇의 설계 및 제어, 협동로봇, 중력보상 로봇, AI 기반 로봇 매니퓰레이션