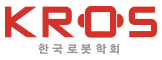
협동로봇 설치작업장 위험성평가 방법 개발 및 규제 대응
© Korea Robotics Society. All rights reserved.
Abstract
Cobots are industrial robots with greatly enhanced safety functions that enable them to work in the same space with workers without protector. Cobots are regulated by the Industrial Safety and Health Act and must be ce.jpgied according to the manufacturing stage, installation stage and usage stage. The ISO 10218-2 standard applied in the installation phase is difficult to apply in the field. Therefore, it is necessary to develop a risk assessment method based on ISO 12100 standard. This paper proposes a new methodology that combines ‘JSA’ and ‘What-if’, which reflects the human error and the lack of known risk factors. Accordingly, a new risk assessment template was proposed and the effectiveness of the developed new template was examined. The current cobot safety regulations need to be unified with safety inspections scheme, and robot safety experts and infrastructures need to be expanded and Robot safety regulations should be unified to ‘Robot Act’. Based on this research, risk assessment methods suitable for the field need to be developed additionally, and robot safety regulation needs to be transformed to promote the industry.
Keywords:
Cobot Workspace, Risk Assessment, Cobot Safety1. 서 론
협동로봇은(Collaborative robot)은 펜스와 매트라는 안전 방호 수단 없이 작업자와 직접 접촉하며 작업공간을 공유하는 안전기능이 대폭 보강된 Cage free형 산업용 로봇이다. 일반적 으로 산업용 로봇은 제어를 위한 프로그래밍 과정을 거치지 만, 협동로봇은 쉬운 작업교시 기능으로 직접 혹은 그래픽 기 반의 입력으로도 작업 명령을 부여할 수 있는 특징이 있다[1].
그러나, 협동로봇은 산업안전보건법 상 위험·기계류로 분 류되어 관리되기 때문에 협동로봇을 설치하여 사용하는 사업 주는 혹시나 모를 산업재해 예방을 위한 동 법 상의 기준들을 준수해야 할 의무를 부여받고 있다. 산업재해 예방 기준 준수 및 좋은 근로환경을 조성해야 할 의무가 있으며(동 법 제5조), 위험·기계류로 분류된 협동로봇을 사용하기 때문에 위험을 예방하는 안전조치(동 법 제23조)를 취해야 할 의무도 있다[2].
이에따라 협동로봇에 적용되는 산업안전보건법 체계 상의 규제들은 [Fig.1]과 같이 제조단계, 설치단계, 사용단계로 나 누어 제조사와 사업주가 각각 적용을 받게 된다[2].
제조사는 제조단계에서 협동로봇 제품 모델별로 자율안전 확인신고(KCs)를 고용노동부에 득하고, 협동로봇 성격의 모 델로 제작되었음을 ISO 10218-1 인증을 통해 획득해야 한다. 이때, 공신력있는 시험인증기관으로부터 3자인증을 획득하 면 안전에 대한 의무가 완료된다[2].
그러나, 문제는 설치단계와 사용단계에서 근로자의 안전을 보장해야 하는 사업주이다. 현행 법 상, 사업주는 협동로봇을 도입하여 설치하는 단계에서 국제표준인 ISO 10218-2(산업용 로봇 시스템 안전)을 제3자로부터 인증을 받아 제시할 수 있어 야 한다. 또한, 최초 설치 후 3년 이내에 안전한지 여부를 ‘안전 검사’를 통해 득하고 이후 2년 주기로 검사를 받아야 한다. [Fig. 2]와 같이 협동로봇은 로봇, 설치된 환경, 운영근로자의 숙련도, 육체적 상태에 따라 다양한 형태의 유해·위험요인이 발생할 수 있으므로 안전여부를 판단하고 조치하기 위한 ‘위 험성평가(Risk Assessment)’가 반드시 필요하다.
협동로봇을 활용하는 작업장에서 ISO 10218-2 표준의 항목 하나하나에 대한 부합성·적합성을 엄밀히 적용하는 방식의 ‘위험성평가’는 어려울 수 밖에 없다. C-type인 ISO 10218-2 표 준은 2011년 최초 제정되었으나, 협동로봇 상용화 전 단계임에 따라 충분한 위험요인에 대한 사례를 담고 있지 않은 문제가 있 다. 또한 현재 국제표준화 방향도 협동로봇 제품 자체 안전성에 만 집중하고 있어, 협동로봇 설치 작업장에 대한 안전성 연구는 미진한 상황도 한몫하고 있다. 따라서, 협동로봇을 활용하는 작 업장의 안전성은 ISO 10218-2 표준 보다 ISO 12100 (Safety of machinery - General principles for design - Risk assessment and risk reduction)의 일반 원칙에 기반한 위험성평가 방법론을 정 립하고 적용해 나가는 것이 현실적 일 수밖에 없다.
따라서, 본 고에서는 협동로봇을 사용하면서 야기될 수 있 는 위험요인(Hazard)을 도출하고 체계적인 위험성 감소 방안 을 마련할 수 있는 ISO 12100 기반의 위험성평가 방법론을 제 시하고자 하며, 아울러 현행 제도 상의 규제 개선 사항을 논하 고자 한다.
2. 위험성평가 개념과 방법
2.1 위험성평가 개념
위험성(Risk)은 [Fig. 3]과 같이 개념적으로 사람과 로봇이 장소적으로나 시간적으로 겹쳐지게 되는 영역에서 발생하며, 위험성은 사람과 로봇이 가까이 접근할수록 커진다[4].
위험성 평가는 산업안전보건법 제41조의2(위험성평가) 조 항에 근거하여 사업주가 사업장의 유해·위험요인에 대해 위 험성평가를 하도록 주문하고 있다. 이를 원활히 시행하기 위 해 고동노동부에서 고시한 ‘사업장 위험성평가에 관한 지침’ 의 해설서에 따르면 위험성평가란 ‘유해·위험요인을 사전에 찾아내어 그것이 어느 정도로 위험한지를 추정하고 그 추정한 위험의 크기에 따라 대책을 세우는 것으로 사고의 미연 방지 가 실시 목적’이라 정의하고 있다[5].
KS B ISO 12100 표준에서는 ‘위험성분석과 위험성 결정/결 과로 구성되는 전체 과정’으로 용어 정의 하고 있는데 위험성 평가에서 사용되는 주요 용어 및 이에 대한 정의는 [Table 1]과 같다[6,7].
2.2 위험성평가 절차
위험성평가는 일반적으로 5가지 단계에 따라 실시하는데 ISO 12100 국제표준을 원칙으로 따른다. 국내에서는 고용노 동부가 제정한 ‘사업장 위험성평가에 관한 지침’을 준거하여 위험성평가에 대한 기본적 절차를 따르고 있다[5].
위험성평가의 첫 번째 절차는 (1) 사전준비(Preparation of R.A.)이다. 본 단계에서는 위험성평가 실시 규정을 작성하고 평가대상을 선정하며 평가팀 구성 및 필요한 관계자 교육을 실시한다. 두 번째 단계는 (2) 유해·위험요인을 파악(Hazards Ide.jpgication)한다. 사업장 순회 점검, 청취조사, 알려진 위험사례 조사 등을 실시하고 일반적으로 4M, JSA등의 위험성평가 방법론 을 적용한다. 세 번째 단계는 (3) 위험성 추정(Risk Estimation)으로 상해의 발생확률(Probability)과 그 심각성(Severity)을 조합하는데 매트릭스법, 분기법, 곱셈법, 덧셈법 등을 사용한다. 네 번째 단 계는 (4) 위험성 결정(Risk Evaluation)으로 위험성 추정결과와 사업장 내에서 허용 가능한 위험성 기준을 비교하여 허용 가 능 여부를 판단한다. 일반적으로 사업장의 특성을 반영하되 설명 가능한 수준에서 허용 가능 기준을 결정한다. 마지막 다섯 번째 단계는 (5) 위험성 감소 대책 및 시행(Risk Reduction & Implementation) 단계인데 제거, 대체, 공학적 대책, 관리적 대 책, 개인 보호구 사용 등의 낮은 단계로 순차적으로 판단하여 시행한다. 위 두 번째 단계부터 다섯 번째 단계까지는 허용 가 능한 안전수준에 이를때까지 계속 반복하고, 완료되면 기록 및 안내 게시하여 마무리하게 된다. 위 5가지 위험성평가 단계 를 도식화하면 [Fig. 4]와 같다[5,6].
2.3 위험성평가 방법론
위험성평가의 기법은 크게 정성적 평가 방법론과 정량적 평가 방법론으로 나눌 수 있다. 정성적 평가 방법론은 체크리 스트법(Checklist), 사고예상질문분석법(What-if), 상대위험순 위법(Dow & Mond Indices), 위험과 운전분석법(HAZOP), 이 상위험도분석(FMECA) 등이 있다. 정량적 평가 방법론은 결 함수분석(FTA), 사건수분석(ETA), 사고영향분석(CA) 등이 있다. 이중 위험기계류에 적용되고 있는 대표적인 정성적 방 법론은 4M법, JSA법, What-if법 등이다[4].
공정 내 잠재하고 있는 유해위험요인을 인적(Man), 기계적 (Machine), 물질·환경적(Media), 관리적(Management) 관점에 서 파악하는 방법이다. 4M법은 안전하고 쾌적한 생산활동 및 지원활동 과정에서 내재된 산업재해발생 위험요인 저감하는 데 활용 가능하다[8].
작업 대상물에 나타나거나 잠재되어 있는 모든 물리적, 화 학적 위험과 작업절차 상 근로자의 불완전한 행동요인을 발견 하기 위한 방법으로 ‘작업안전분석(Job Safety Analysis)’으로 불린다. 보통 작업방법을 변경할 경우 적용하고 이를 작업절 차서 지침서 등에 반영한다. JSA는 표준운전절차(Standard Operating Procedure; SOP) 및 동일한 작업이 반복되는 경우 활 용도가 높다[4].
주로 공정 및 설비의 이상과 공정 변화 시에 적용하는데 원 치 않는 사건에 대한 질문(What-If)를 던짐으로서 잠재하는 위 험성을 도출하는 방법이다. 공정의 개발단계, 초기 시작단계 에 유용하게 적용되며, 쉬운 적용과 빠른 결과의 도출이 장점 이다. 그러나, 체계성은 낮고, 공정에 대한 전반적인 이해가 있 는 숙련자가 시행해야 하는 한계가 있다[4].
공정 및 설비의 오류, 결함상태, 위험상황 등을 목록화한 형 태로 작성하여 경험적으로 위험성을 비교 평가하는 방법이다. 관련 전문가들의 경험에 기반을 두기 때문에 미숙련자도 일반 적인 위험 요소들을 손쉽고 빠르게 확인할 수 있는 장점이 있 지만, 위험성 평가의 최소 수준만 보기 때문에 누락되거나 형 식적 수행이 이뤄질 단점도 가지고 있다[5].
3. 협동로봇 설치작업장 위험성평가 방법 개발
3.1 개발 방향
국내에 본격적으로 협동로봇 제품이 도입된 것이 2017년부 터임을 고려할 때, 협동로봇 설치작업장(Cobot Workplace) 에 대한 사고나 상해에 대한 정보가 누적될 만한 시간은 아니므 로 위해·위험요인(Hazard)에 대해 축적된 내용은 많지 않다. 따라서, 협동로봇 설치작업장 내에서 적용할 만한 위험성평가 방법은 정립되어 있지 않은 상황이므로 개발을 위해 고려해야 할 사항을 제안하면 다음과 같다.
첫째, 협동로봇 설치작업장은 알려지거나 축적된 사고, 상 해 등의 정보가 없는 새로운 영역이므로 이를 고려할 때, 상식 적으로도 타당한 방식을 적용하여야 한다. 둘째, 협동로봇의 특성 상 저속, 저하중이므로 로봇자체에 의한 끼임, 충격 등의 사고보다는 근로자의 실수(Human Error)에 의한 사고일 가능 성이 높으므로 근로자의 작업 행동 과정을 고려한 방법이 개 발되어야 한다. 마지막으로 실제 협동로봇이 가진 태생적 전 제 상, 중소기업이 대상이 될 가능성이 높으므로 사업장내 위 험성평가 시행 및 관리의 경험이 부족할 가능성이 높다. 따라 서, 생산성 향상, 근로조건 개선을 위한 목적으로 도입하는 중 소기업의 입장에서 위험성평가 방법을 합리적이면서도 보다 손쉽게 할 수 있어야 한다. 세가지 조건은 상호 균형적인 영향 을 이뤄야 한다. 이를 정리하여 도식화하면 [Fig. 5]와 같다.
3.2 모델 개발
개발 방향과 같이 협동로봇 설치작업장에 대한 위험성평가 방법은 알려지지 않은 위험원을 도출할 수 있어야 하며 근로 자 작업 행동 중심의 쉬운 방식이어야 한다. 이에 따라, 기존의 위험성평가 방법론 중 이에 부합된 2가지 방법론을 혼합하여 새로운 모델(Cobot R.A. Model)을 만들고자 한다. 이를 위해 국내 최고의 산·학·연 전문가 9인으로 구성된 개발위원회를 구성하고 4차에 걸친 워크숍을 통해 개발을 추진하였다.
먼저, (a) 근로자의 작업 실수를 최소화하기에 적합한 방법 인 ‘JSA (Job Safety Analysis)’를 준용하였다. JSA 방식은 작업 자의 행동 과정을 중심(Behavioral)으로 분석하며, 대상 공정 의 작업 순서를 5-6개 내외로 나누고 각 과정에서 발생하는 알 려진 위험원을 점검하고 감소대책을 수립하는 방법이다. 두 번째로, (b) 어떤 것이 위험한지 축적되지도, 알려지지도 않은 경우(unknown) 에 쓰이는 방법이 ‘What-If’ 방식을 준용하였 다. 이때, 위험성평가 절차 상 구성되는 평가팀의 위험원 도출 을 위한 브레인스토밍이 중요하다. 되도록 조직 내에서 공정 운영 경험이 많은 구성원이 포함되어야 하며, 고장 등 관리를 하는 공무팀 직원이 참석하는 것이 좋다. 위 두가지 방식은 쉬 운 적용과 익숙한 공정에 대한 이해를 바탕으로 하고 있기 때 문에 활용이 용이하다. (c)다음 단계는 일반적인 위험성평가 의 절차에 따라 시행하면 된다. [Fig. 6]은 두가지 기법을 융합 한 새로운 위험성평가 템플릿 개념 설명이다.
대부분의 경우, 최초 평가 단계에서 대다수의 위험요인들 과 위험한 사건이 도출 될 수 있으므로 본 모델에서는 최초평 가에 적용되는 ‘(1) 위험성 추정 및 결정’ 템플릿과 위험성 감 소대책 중심의 ‘(2) 위험성 결정에 따른 위험성 감소대책 시행 결과’ 템플릿 2종으로 나누어 개발하였다. ‘(1) 위험성 추정 및 결정’ 템플릿은 ‘JSA + What-If’ 조합에 따른 위험요인 도출에 주안점을 두었고, ‘(2) 위험성 결정에 따른 위험성 감소대책 시 행 결과’ 템플릿은 허용 가능한 수준의 위험성까지 반복 사용 하는데 초점을 두고 있다. 이때, 이미 위험성 감소조치가 완료 된 위험한 사건도 반복 기술하게 되는 문제가 있을 수 있으므 로 두 번째 템플릿부터는 완료된 사안을 제외하고 기술하되, 식별번호로 구분될 수 있도록 하였다. [Fig. 7]은 개발된 2종의 템플릿 및 이를 활용하여 적용한 부분적 사례인데, 온라인 상 공개된 협동로봇 작업 공정을 샘플로 적용하여 위험성평가에 효과적으로 활용될 수 있는지 확인하였다[9].
대상공정은 협동로봇을 활용한 샴푸 용기 포장 및 이적제 공정으로 작업자와 협동로봇이 순차적으로 작업을 진행한다. JSA방법에 따라 작업 절차는 크게 4단계로 구분하였고 각각 의 단계별로 위험한 사건을 What-If 방식으로 도출하였다. 브 레인스토밍을 통한 위험한 사건의 도출(발견)은 템플릿을 개 발한 전문가 그룹이 평가팀이 되어 실시하였으며, 위험성평가 절차에 따라 진행하였다. 상해발생 가능성과 상해심각성을 각 각 3등급 척도로 부여하였고 이를 매트릭스 방식에 의해 위험 성 추정 및 결정을 실시하였다. 위험성 결정 단계에서 허용 가 능한 위험한 사건은 제외하고 허용 불가능한 위험한 사건만을 대상으로 위험성 감소대책을 도출하고 그 결과를 해당 템플릿 에 기록하였다. 일반적으로 위험성평가에 사용하는 4M 방식 보다는 작업자 행동 중심의 위험한 사건이 상대적으로 많이 도출되어 [Fig. 5]의 개발 방향대로 위험성 평가가 이뤄지는 것 을 확인하였다.
4. 안전규제 대응 방향
현행 협동로봇 안전 관련 규제는 신기술이 시장에 도입되 면서 나타나는 알려지지 않은 위험을 어떻게 대응하고 다뤄가 야 하는지 실증하는 좋은 사례이다. 실제 정부의 규제개혁 추 진에서도 협동로봇 규제 개선을 선결 과제화 하여 추진하였 다. 그러나, 여전히 해결해야 하는 문제가 몇가지 있다.
첫째, 다른 품목의 안전 규제와 달리 협동로봇은 단계별로 획득해야 하는 인증이나 기준이 많은 편이다. 실제 안전사고 등의 문제는 사용하는 단계에서 많이 발생하는 만큼 설치단계 에서의 인증은 안전증빙 서류 확보 형태로 전환하고 안전검사 단계에서 이를 확인하는 방식으로 통합을 검토해야 한다. EU, 일본 등의 경우 산업용로봇 안전관리는 자기적합성 선언을 기 반으로 운영되고 있음을 감안할 때, 설치단계 만이라도 위험 성평가 서류완비에 따른 자기적합성 선언 방식으로 허용이 필 요하다.
두 번째, 협동로봇 등 로봇 안전 관련 인프라와 인력 확보가 필요하다. 로봇을 활용한 다양한 서비스가 확산될 것으로 예 상되고 있는 상황에 비례하여 알려지지 않은 위험 역시 증가 될 것이다. 최근 우리 사회 역시 안전에 대한 문제가 부각되고 있는데 이것은 곧 제도적 규제로 연결될 가능성이 높은 주제 이다. 따라서, 공학적 대책을 마련한다든지, 제도적 보완 정책 수립, 표준 제정을 통한 안전 활용 기준 마련 등을 전문성 있게 추진할 수 있는 인프라와 인력을 확보해 나가야 한다.
세 번째, 로봇공학 분야와 안전공학 분야의 융합이 가속화 될 필요가 있다. 두 분야 모두 표준화, 인증 등 유사한 산업화 체계를 가지고 있지만, 실제 사용하는 용어는 다소 차이가 있 다. 실제 KS표준의 국제표준 부합화 단계에서도 추진 주체에 따라 용어와 해석이 달라지는 문제가 발생하고 있다. 따라서, 용어표준화 등을 위한 교류와 협력이 필요한 시점이다.
마지막으로 법적 거버넌스의 재정립이 필요하다. 현재 로 봇산업 육성을 위한 근거법으로 ‘지능형로봇 개발 및 보급촉 진법’이 있고, 로봇을 사용하는 사업장 등의 안전 사항은 ‘산 업안전보건법’에 의해 다뤄지고 있다. 두 법의 취지가 상이한 문제가 있어 언제든 진흥 이슈와 규제 이슈가 상충될 가능성 이 존재한다. 시장초기 상황인 만큼 로봇산업은 규제보다는 진흥정책을 통해 성장하는 것이 우선적일 수 있다. 따라서, 로 봇법에 안전 관련한 규제를 담아 행정 거버넌스를 일원화하고 산안법은 로봇법에 따른 안전조치 결과를 인정하는 협업 체계 로 가는 것을 제안 한다.
5. 결 론
협동로봇은 글로벌 경쟁력을 가질 수 있는 산업용로봇의 틈새 시장으로, 이를 국내에 보급 활성화하기 위해서 산업안 전보건법이 요구하는 안전 조건을 충족시켜야 한다. 따라서, 설치 단계의 중소기업 작업장에 보다 용이하고, 합리적 수준 에서 위험성평가 방법이 도입될 필요가 있다.
이를 위해서 타 산업에서 활용되어 왔던 위험성평가방법의 장점을 조합한 새로운 형태의 협동로봇 설치작업장 위험성평 가 방법을 제시하였다. 그러나, 모든 작업장에 획일적으로 적 용될 수 있는 위험성평가 방법은 있을 수 없다. 본 고에서 제시 된 방법을 시작으로 작업환경에 맞는 위험성평가방법이 창의 적으로 적용될 필요가 있다. 또한, 로봇 안전 규제 역시 산업을 진흥하는 방식으로 적용 될 필요가 있다. 당위적 규제로만 문 제를 다루고자 한다면 근로자의 안전한 근로환경 구축이라는 당초의 취지는 희미해지고, 상황을 면하고자 하는 일회적 요 식행위로 흘러갈 가능성이 높다. 본 연구가 로봇 안전 제도의 고도화 및 유·무형 인프라 확충의 추동으로서 또한, 국내 협동 로봇 시장의 활성화에 작게나마 기여하길 기대한다.
Acknowledgments
This project was funded by the Ministry of Trade, Industry & Energy (Project No, 10084657, Development of functional safety technology and Risk Assessment / Reduction technology based on International Standards related to safety of robots operating in human contact environment)
References
- J. W. Jun, “Era of Cooperative Robots Working with Humans,” KOITA Technology & Innovation, vol. 418, pp. 25-27, Jun., 2018.
- “Special course for training safety ce.jpgication Auditor at Cobot Workspace,” KIRIA, Deagu, South Korea, 2019, pp. 3-36, 2019.
- Delmiablog, Collaborate, Model, Optimize, Perform, [Online], https://blogs.3ds.com/delmia/2017/12/the-value-of-simulation-for-collaborative-robots-part-i/, Accessed: May 7, 2017.
- J. T. Song and J. W. Lee, “Risk Assessment and Analysis Techniques Based on PSM,” Risk Assessment and Analysis Techniques, SungAnDang, 2017, ch . 2, pp. 154-223.
- “Guide to Risk Assessment,” KOSHA, Ulsan, South Korea, pp. 1-92, 2019.
- Safety of machinery -General principles for design- Risk assessment and risk reduction, ISO 12100, Oct. 20, 2010.
- Robots and robotic devices — Safety requirements for industrial robots -Part 2: Robot systems and integration, ISO 10218-2, Jul. 1, 2011.
- J. T. Song and J. W. Lee, “Other Risk Assessment and Analysis Techniques,” Risk Assessment and Analysis Techniques, SungAnDang, Seoul, South Korea, 2017, ch. 4, pp. 434-447.
- Andrewdonalddesign, ADDE Baxter Lab Case Packing and Palletising, [Online], https://www.youtube.com/watch?v= pO09vPELQmM, Accessed: Dec. 27, 2017.
1996 성균관대학교 생기전공학과(공학사)
2003 상명대학교 기술경영학과(석사)
2010~현재 로봇산업진흥원 수석연구원
2013~현재 로봇분야 KS 전문위원
관심분야: 로봇안전, 로봇 기술정책, 로봇 표준인증
2013 한양대학교 전자공학과(공학사)
2013~현재 한국로봇산업진흥원 선임연구원
2014~현재 ISO TC299, IEC TC62 Member
2018~현재 ASTM F45, F48 Member
관심분야: 로봇안전 ,협동로봇, 웨어러블 로봇, 의료로봇
2002 한남대학교 화학공학과(공학사)
2013 전남대학교 신소재공학과(공학석사)
2010~현재 전남테크노파크 선임연구원
관심분야: 바이오-농업용 로봇, 협동로봇, 빅데이터, 스마트공장