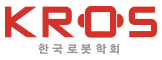
급속 확산되는 물류현장의 로봇적용 사례
CopyrightⓒKROS
Abstract
Logistics industry still heavily relies on human labor in many field processes. However, robot applications in logistics are rapidly increasing, encouraged by technological progresses in robotics and cheaper robot solutions from competition between robot suppliers. Effectiveness of logistics automation are higher productivity for cost reduction and increased process capabilities for better profit, which is witnessed in many fields of logistics industry. In this paper, differences in logistics services – contract logistics, parcel, and fulfillment – are addressed, and characteristics and issues in application of various kinds of logistics robots such as AGV, AMR, ASRS, box/piece handling robots and robotic wearable devices are discussed. The advantages from flexibility and scalability of logistics automation by robots will benefit the future logistics business.
Keywords:
Logistics Robot, Logistics Automation, AGV, AMR, Robot Box Handling, Robot Piece Picking, Robotic Truck Unloading, Robotic Wearable Device1. 서 론
물류업은 아직까지 많은 현장에서 노동집약적 산업으로 남아있는 것이 현실이다. 오래 전부터 자동화에 대한 연구와 투자가 진행된 제조업은 공정별로 다양한 형태의 로봇이 투입되어 인력 의존도를 낮춘 반면, 물류 현장은 다양한 종류의 화물을 정해진 시간 내에 빠르게 핸들링 해야 하는 기술적 어려움으로 인해 로봇으로 대체 가능한 프로세스가 한정적이고, 하루 중 일부 시간에만 가동해야 하는 비즈니스 특성으로 인해 투자 대비 효과가 크지 않아 상대적으로 자동화 수준이 매우 낮은 상황이다.
최근 이커머스의 성장 및 경쟁심화, 인건비 상승과 노동인구 감소에 따른 인력 소싱 난이도 증가, 다양한 배송 서비스에 대한 소비자 기대 증가 등 물류사업 환경의 급격한 변화로 인해, 물류의 디지털 전환, 특히 로봇의 활용이 가속화되고 있다[1].
더욱이 로봇 기술의 발전과 로봇 공급 업체의 증가, 보다 저렴해진 로봇 및 관련 기술 공급가에 따라 전세계 곳곳의 물류 현장에서 생산성 개선, 처리능력의 증대, 작업자 업무 부하 감소 등의 자동화 효과가 확인되고 있다.
본 논문에서는 물류 현장에 급속 확산되는 로봇 적용 사례와 더불어 로봇의 형태별 특징과 해결과제를 소개하고 로봇의 적용을 통해 변화되는 앞으로의 물류센터의 모습을 제시하고자 한다.
2. 물류 비즈니스 모델과 자동화 니즈
2.1 물류 서비스 제공 형태
종합 물류기업의 물류 서비스 제공 형태는 계약 물류(Contract Logistics), 택배, 풀필먼트(이커머스 물류), 포워딩, 항만하역/운송 등이 있다. 이 중에서 계약 물류, 택배, 풀필먼트 3가지가 로봇을 이용한 자동화와 연관이 많으므로, 3가지 서비스 영역에 대해 비즈니스 모델의 특성과 적합한 로봇의 종류 및 적용 형태에 대해 설명하려 한다.
2.2 계약 물류(CL, Contract Logistics) 서비스
기업간 거래(B2B) 구조로, 고객 기업의 니즈에 따라 맞춤형 물류 서비스를 제공한다. 고객이 위탁한 상품의 보관, 피킹, 출고, 배송 등을 수행하며 제3자 물류(3PL, 3rd Party Logistics)로도 불린다.
대부분 상품의 제조사 또는 수입처로부터 물류센터로 입고될 때에는 여러 박스를 적재한 팔레트 단위로 공급되고, 물류센터 내의 팔레트 랙에 팔레트 단위로 보관되는 것이 매우 일반적이다[Fig. 1]. 배송처로부터 접수된 주문에 따라 분류되고 배송되는데, 팔레트, 박스 단위로 공급되는 경우가 가장 많지만, 국내에서는 낱개 단위(박스에 들어있는 개별 상품 단위) 주문 요구도 많아서 낱개 단위의 취급도 필요로 한다. 입고될 때에는 종이 박스에 담겨 오지만, 고정적인 배송처를 갖고 있는 것이 일반적이라 재사용이 가능한 회수용 박스에 담겨 출고되기도 한다.
상품을 입고할 때에는 지게차를 이용하여 트럭에서 하차하는 경우가 일반적이고, 보관할 때에도 주로 2~5단 높이의 팔레트 랙에 적치되므로 지게차가 활용된다. 하차 작업과 적치 작업에 무인 지게차를 활용할 수 있으며, 팔레트 랙 대신에 팔레트의 입출고가 가능한 ASRS (Automated Storage and Retrieval System)에 상품을 보관하기도 한다.
분류 작업은 최소한 박스 단위로 이루어지므로, 팔레트에 쌓인 박스를 하나씩 들어 옮기는 디팔레타이징, 분류된 박스를 출고지 별로 자동 분류하고 쌓는 팔레타이징 등에 3D 비전 시스템과 로봇 팔을 이용할 수 있다. 대량의 박스 분류를 위해서는 바코드 인식장치와 휠소터 또는 크로스벨트 소터가 설치된 컨베이어 시스템을 주로 활용해 왔는데, 최근 AGV를 활용하여 유연성이 높은 분류 시스템이 소개되고 있다.
낱개 분류가 필요한 현장에서는 낱개 단위 자동분류 장치가[Fig. 2] 활용되었지만, 최근에는 소형 AGV를 활용하기도 한다. 낱개 단위 취급을 완전 무인화 하는 방법으로는 3D 비전과 AI 알고리즘을 이용한 로봇 낱개 피킹을 활용할 수 있지만 아직 보편화되지 않고 있다.
CL 사업에서 고객과의 계약 기간은 투자 규모와 형태에도 영향을 준다. 계약 기간 중에 활용한 자동화 설비가 계약 종료 후에 쓸모가 없어질 수도 있기 때문에 컨베이어, 소터 등 고정 설비 보다는 AGV, AMR 같은 이동 로봇이 투자의 유연성 측면에서 장점이 있다.
2.3 택배(Parcel) 서비스
포장이 완료된 고객의 화물을 발송지에서 집화하여 목적지별 분류 작업을 거쳐 최종 목적지까지 배송하는 서비스를 제공한다.
해외에서는 주로 종이 박스와 폴리백 등으로 포장된 택배만 배송하는데, 국내에서는 냉동/냉장 식품의 배송도 흔하기 때문에 종이 박스, 폴리백 외에도 스티로폼 등 다양한 형태의 화물을 취급하고 있다.
택배는 화물을 최종 목적지까지 빠르게 배송하는 것이 주된 목적이기 때문에 물류 현장에 임시 보관 외에는 화물의 보관 공간을 마련하지 않고 주로 분류, 상하차에 공간을 할애한다[Fig. 3].
대량의 화물을 저렴한 비용으로 한정된 시간 내에 분류하고 배송하는 것이 매우 중요하다. 화물의 수집과 배송이 시작되는 거점의 개수가 적을 때에는 각 거점을 Point-to-Point 형태로 배송하는 네트워크가 유리하지만, 거점 개수가 늘어나면 경제성 측면에서 수집과 배송의 거점(서브 터미널)을 분류 전담 거점(허브 터미널)과 연결하는 Hub-and-Spoke 방식의 네트워크를 채택할 수밖에 없다.
서브 터미널과 허브 터미널 사이에 화물을 운송하는 간선 트럭은 국내에서 일반적으로 11톤 트럭이 활용되는데, 한번에 약 2천개의 화물을 운송할 수 있다. Hub-and-Spoke 방식의 택배 네트워크 구조에서는 서브 터미널과 허브 터미널에서 상차와 하차 작업을 각각 한번씩 수행해야 하고, 목적지별로 분류하는 작업이 이루어진다. 분류 작업은 바코드 인식장치와 휠소터 또는 크로스벨트 소터를 활용해서 자동화가 되어 있지만, 택배 화물의 하차, 상차 작업은 아직 기술적인 난이도가 매우 높아 수작업으로 이루어지고 있다.
특히 화물을 차에서 싣고 내리는 상하차의 경우, 작업자의 업무 강도가 가장 높은 작업으로 상하차 로봇의 개발/활용을 통한 자동화가 필수적인 영역으로 손꼽힌다. [Fig. 4]에서와 같이 박스의 형태로만 들어오는 경우도 있으나, 대부분의 택배 사업 현장에서는 박스, 파우치(비닐), 마대를 동시에 다루기에, 작업자도 매번 바뀌는 물성을 대응하기 위해 다양한 방법으로 상품을 상/하차 해야하는 상황이다. 이는 로봇을 적용하는데 있어서 상품을 인식/파지를 위한 포지셔닝을 하기에 고난이도 기술이 요구되는 이유이기도 하다. 박스 형태의 상품을 상/하차 하는 시스템은 컨셉츄얼하게 개발된 사례[2]가 있으나, 대한민국 택배 시장에서 사용되는 다양한 형태의 물성을 소화하는 사례는 찾아보기 어렵다.
로봇 기반의 완전 자동화를 위해서는 기술된 여러 난제들을 풀어야 하는 만큼, 작업자의 근력 보조를 위한 웨어러블 로봇 또한 크게 주목받고 있다.
2.4 풀필먼트(Fulfillment) 서비스
이커머스 플랫폼에 입점한 판매자의 상품을 물류 현장에 보관했다가, 소비자의 온라인 주문에 맞춰 상품을 피킹, 분류, 포장하여 배송하는 등 이커머스 물류 전체를 서비스하는 모델이다.
물류센터에서 상품을 보관, 피킹, 포장하는 프로세스는 CL과 동일하고, 포장이 완료된 상품을 소비자에게 배송하는 프로세스는 택배와 동일하므로 CL과 택배가 결합된 형태이다.
풀필먼트는 온라인에서 판매되는 수백~수천 가지의 상품을 빠르게 처리해야 하며, 요일, 계절, 날씨, 판매 할인행사 등 요인에 따라 소비자의 주문량이 크게 변동되고 사전 예측이 어려워 일정한 서비스 품질 수준을 유지하는 것이 큰 도전 과제이다. 또한, 낱개 단위의 상품을 취급해야 하기 때문에 물류 작업의 복잡도가 높아 아직까지 많은 프로세스가 수작업에 의존하고 있다.
기존에는 상품 피킹/분류를 위해 DPS (Digital Picking System)/DAS (Digital Assorting System)[3]와 같이 컨베이어를 활용한 고정식 설비를 주로 활용했지만, 물량의 변폭이 크고 물류 서비스가 계약된 판매자 마다 다양한 물성의 변화도 대응하기 위해 최근에는 AGV, AMR 등 유연성이 높은 로봇을 활용하는 사례가 늘어나고 있다.
수많은 종류의 낱개 단위 상품을 효과적으로 보관, 피킹 하기 위해 ASRS, 무인 풀필먼트 구현을 위한 낱개 피킹 로봇 등의 활용 또한 중요한데, 그에 대한 기술별 상세 내용은 3장에서 다루기로 한다.
2.5 물류 비즈니스 모델별 자동화 니즈
본 장을 종합했을 때 물류 비즈니스 모델별 물류 특성과 자동화 니즈를 다음과 같이 요약할 수 있다.
계약물류과 풀필먼트의 경우, 물류센터 내에서 박스를 자동으로 이재/적재함으로써 단순 반복적인 고강도 작업을 대체하는 것이 필요하다.
반면 택배의 경우 허브/서브 터미널에서 대량의 화물을 자동으로 빠르게 분류하고, 차량에 싣고 내리는 상하차(Loading/Unloading)의 자동화가 중요하다.
3. 물류 로봇 종류별 특징
3.1 물류 로봇의 종류
물류 현장에서 쓰이는 로봇은 그 목적과 특성에 따라 [Table 1]과 같이 다양한 형태로 나눠지는데, 여기서는 물류 현장에서의 적용 프로세스에 맞게 로봇을 이송 자동화, 핸들링, 기타의 3가지로 나누어 소개하고자 한다.
3.2 이송 자동화 로봇
물류센터가 대형화되면서, 상품을 긴 거리로 이송하는 일이 빈번하게 발생되고 있다. 이러한 이송작업은 로봇으로 충분히 대체가 가능한 작업이다. 이로 인해 이동로봇의 도입으로 전체적인 생산성을 크게 높일 수 있다.
바닥에 격자 형태로 부착된 QR 코드를 따라 주행하면서 낱개 상품 피킹을 지원하는 AGV는 한때 아마존에서 독점적으로 활용했으나 이제는 다수의 중국 AGV공급사에 의해 물류현장에 급속도로 확산되고 있다.
가장 보편적인 형태는 CL과 풀필먼트 사업에 주로 활용되는 Pod 이송형 AGV인데, 보통 500~1,000 kg을 이송할 수 있는 AGV이다[4]. 여러가지 낱개 상품은 Pod에 무작위 순서로 보관되어 있다가, 풀필먼트 주문처리 순서에 따라 해당 상품이 담긴 Pod를 피킹 스테이션에 자동으로 공급하는 방식으로 동작하면서, 기존의 수작업 오더피킹 보다 훨씬 생산성을 높일 수 있다[Fig. 5].
기존의 수작업 오더피킹은 상품이 보관된 보관랙 사이를 작업자가 주문지 또는 픽업 순서를 지시하는 태블릿을 들고 여러 주문의 박스를 담을 수 있는 카트를 끌고 다니며 피킹 하는 방식이다[5]. 상당히 넓은 공간을 작업자가 직접 걸어 다니면서 작업하기 때문에, 때로는 피킹에 소요되는 시간보다 이동하는 데 걸리는 시간이 훨씬 많다. 주문량이 적은 경우와 자동화 투자를 최소화할 경우에는 여전히 사용되고 있는 방식이다[Fig. 6].
Pod 이송용 AGV의 경우 작업자가 직접 상품을 꺼내야 하므로 Pod의 높이가 2.5 m 정도 밖에 되지 않는데, 층고가 11 m에 해당하는 최근 건축된 물류 센터에서는 공간효율이 낮은 문제가 있다. 이를 개선하기 위해 매자닌(중간층)을 건설하기도 하지만 건설 비용과 추가적인 인허가 등 부수적인 비용이 소요된다.
기존의 AGV를 플랫폼으로 하면서 새롭게 고안된 시스템으로는 고단의 고정식 경량랙에 상품을 보관하는 셔틀 AGV[Fig. 7]가 있다. 5~10 m 높이까지 상품 보관랙을 높일 수 있어서 보관 공간의 효율을 높이면서, 상품을 피킹 작업자에게 공급되는 방식은 뒤에 설명할 ASRS와 유사해서 여러가지 장점을 갖고 있는 시스템이다. 바닥에 QR 코드를 기준으로 주행하는 AGV 플랫폼은 동일하지만, AGV 위에 수직으로 움직이는 레일과 수평으로 움직이는 로봇팔을 갖고 있어서 경량랙에 보관된 종이박스나 토트를 반출할 수 있다. 반출된 박스는 AGV가 자동으로 피킹 스테이션으로 공급되어 피킹 작업자가 풀필먼트 작업을 수행하는 방식이다.
물류 현장의 또 다른 형태의 AGV는 분류용 AGV이다[Fig. 8]. 주로 소형 상품의 분류 작업을 위해 적재하중 20 kg 이하, 가로 세로 60 cm×60 cm 정도의 소형이 많지만 보다 중량 화물의 분류에 적합하게 만들어진 제품도 있다. AGV 상단에는 크로스벨트나 틸트 트레이가 장착되어 있어서 분류용 박스나 슈트에 화물을 공급한다. 기존의 컨베이어와 휠소터 또는 크로스벨트 소터를 대신하면서 물류 현장의 공간을 자유자재로 변형하여 사용할 수 있어서 유연성과 확장성이 높은 이점이 있다. 이러한 분류용 AGV는 CL, 택배, 풀필먼트 사업 현장에서 폭넓게 사용되고 있다.
위에서 언급한 AGV를 기본으로 최근에는 이를 다양하게 혼합하여 활용하는 물류 자동화 솔루션이 개발되고 있다. 이러한 AGV는 물류센터의 레이아웃에서 AGV 작업공간에 대한 설계, 바닥면 평탄도 기준을 맞추기 위한 추가 공사 등으로 물류센터를 오픈하기 전에 수개월의 리드 타임이 소요되는 것이 일반적이다. 그렇지만, 기존의 고정식 컨베이어와 소터 등에 비해 유연성과 확장성이 높은 장점으로 인해서 최근 물류현장에서 빠르게 확산되고 있다.
AMR (Autonomous Mobile Robot)은 비전과 LIDAR 센서를 활용한 SLAM (Simultaneous Localization and Mapping) 기술로 주행하기 때문에 AGV처럼 인공적인 표식을 부착할 필요가 없는 장점이 있다. AGV는 QR 코드 위로만 주행하고 회전할 때 90도 단위로 회전하는 반면, AMR은 이러한 제약이 없고 동적 장애물 회피가 보다 유연하게 되기 때문에 좁은 공간에서 활용 가능하고 무엇보다도 작업자와 AGV가 동일한 공간에서 함께 작업할 수 있는 장점이 있다. 이러한 점은 화주와 계약 기반으로 이루어지는 CL, 풀필먼트 사업에 적용하기에 매우 적합하게 만들어 준다. 물동량이 적은 계약 초기에는 수작업으로 피킹하다가 어느 정도 물동량이 올라온 다음 AMR을 투입하여 생산성을 끌어올릴 수 있기 때문이다.
AGV는 Pod 이송형, 셔틀 AGV, 소팅 AGV 등 일반적으로 작업 형태가 정형화된 반면, AMR은 AGV 보다 훨씬 자유로운 형태로 사용되고 있다.
오더피킹 현장에서는 피킹 작업자들이 카트를 끌고 이동하는 대신에, AMR에 주문 박스를 탑재하고 각 피킹 위치로 순차적으로 이동시키고, 일정한 구역 마다 할당된 피킹 작업자가 하나씩 피킹하고 다음 피킹 위치로 보내는 방식으로 활용할 수 있다[Fig. 9]. 이 외에도 복잡한 물류 현장에서 화물이 담긴 롤테이너 등을 끄는 방식으로 장거리 이송 활동[Fig. 10]을 대신하는 등 다양한 형태로 활용될 수 있다. 물류산업 시장분석 기업 LogisticsIQ에서는 지금까지는 물류 현장에서 AGV가 더 많이 적용되었지만 2027년부터는 AMR의 적용이 더 많아질 것으로 전망하였다[6]. 물류센터에서의 AMR과 AGV의 가장 큰 차이점은 피킹 스테이션의 위치라고 볼 수 있다. AMR은 AGV와 다르게 사람 및 지게차 등과 함께 운용할 수 있는 강점이 존재하기에, AGV와 같이 고정형 피킹 스테이션이 아닌 실제 작업자가 사용하던 피킹 환경을 사용할 수 있다.
AMR의 활용을 통해 작업자와 로봇의 역할 분리가 명확하게 이루어져, 각자의 장점을 최대한 발휘할 수 있다. 하지만 센싱 기술이 아직까지는 완벽한 안전을 담보하지 못한 부분과, 다수의 AMR을 효율적으로 관제하는 FMS (Fleet Management System) 성능에 따라 로봇 성능이 달라지기에 효율적인 경로계획, 장애물 회피 방안 그리고 로봇 관제 대응 수량 등이 지원되어야 하는 특징이 있다[7].
ASRS는 로봇을 활용하여 화물의 보관과 분출이 자동화된 시스템으로 로봇 이동 통로를 최소화하여 밀집된 공간에 다량의 SKU (Stock Keeping Unit, 상품 보관 단위) 보관이 가능한 장점이 있다.
셔틀형 ASRS[Fig. 11]는 상품이 보관된 통로 사이를 AGV가 수평 방향으로 주행하고, 별도의 수직이동용 리프트가 AGV를 수직 방향으로도 이동시켜 결과적으로 AGV가 전방향을 이동하면서 상품 보관/적재를 수행한다. 셔틀형 ASRS의 대표적인 사례로 KNAPP 사의 OSR shuttle 시스템이 있다. 이 시스템은 통로 공간으로 AGV를 이동시켜 토트 적재/반출 작업을 수행한다[8].
그리드형 ASRS는 상품이 담긴 토트를 통로 공간 없이 3차원 그리드 형태로 배치하고, 랙 최상단에 위치한 로봇이 필요한 토트를 하나씩 꺼내도록 설계하여 보관 공간효율을 극대화하였다. 이들은 선입 선출에 대한 지속적인 재고 재배치를 통해서 다량 SKU의 처리 속도를 높일 수 있다. 그리드형 ASRS의 대표적인 사례로 AutoStore와 Ocado 등이 있다[9].
3.3 핸들링 로봇
물류센터의 개선을 위해 중요한 작업 중 하나는 핸들링 자동화이다.
핸들링이란 박스 혹은 상품을 집어 이동시키는 등 피킹의 모든 행위를 의미하며, 주문 건에 대한 출고를 위한 피킹, 재고 보충을 위한 피킹 등과 같이 목적에 따라 다양한 피킹 행위를 하게 된다. 피킹 작업은 작업의 복잡성에 의해 대부분 작업자가 하게 되는데, 그 중 단순하고 작업 시 위험성이 높으며, 반복성이 높은 작업들부터 점차 로봇으로 대체되어 가고 있다[Fig. 12]. 이러한 피킹 프로세스의 자동화를 위해 다양한 핸들링 로봇의 개발이 요구된다.
박스 핸들링 로봇은 박스를 팔레트 위에서 피킹 및 컨베이어 투입을 하는 디팔레타이징 로봇과 일정하게 공급되는 박스들을 팔레트 위에 적재하는 팔레타이징 로봇으로 나눌 수 있다.
제조 현장에서는 팔레트 위에 동일한 상품이 정형 패턴으로 적재된 경우가 많지만, 물류 현장에서는 팔레트 위에 사이즈가 다른 상품이 다양한 패턴으로 적재된 경우가 흔하다. 이런 사유로 제조 현장의 디팔레타이징 로봇 대비 물류 현장의 로봇이 개발 난이도가 높으며, 자체 학습기능을 통해 지속적으로 바뀌는 박스를 핸들링 할 수 있어야 한다[10]. 디팔레타이징 로봇과 함께 팔레트의 공급을 AGV, AMR 등으로 자동화하면[Fig. 13] 작업물 투입을 위해 작업자가 대기하는 시간을 줄여 더욱 큰 생산성 개선 효과를 낼 수 있다.
팔레타이징 로봇도 제조 현장에서는 널리 사용되고 있지만, 규격화된 박스를 정형패턴으로 적재하는 솔루션으로 상용화 되어 있다. 물류현장의 팔레타이징 로봇은 공급되는 박스를 출고 혹은 이송하기 위해 무작위 순서로 공급되는 다양한 종류의 박스를 팔레트 위에 안정되게 적재하는 기능이 필요하다.
팔레타이징 로봇에는 박스의 구분을 위한 바코드 인식, 박스의 체적정보 측정, 체적 정보 기반 적재 팔레트 내 적재 위치 도출 등의 작업이 요구된다. 디팔레타이징 로봇과는 다르게 착지 구분 및 적재 위치 도출이 요구되어 적재 알고리즘[Fig. 14]이 필수적인 사유로 상용화 된 사례가 부진한 상태이다.
현재 팔레타이징 로봇의 수준은 단일 착지 및 물성 정보의 사전 제공 기준으로 상용화되어 있다. 이는 비정형 및 이형 박스의 적재가 가능한 수준이지만, 다수 착지 및 무작위 배출에 대해서는 적재가 불가한 상황이다. 이에 팔레타이징 설비가 물류 현장에 적용되기 위해서는 다양한 특성을 가진 화물의 핸들링과 적재 위치 그리고 도출된 위치에 대한 정확한 적재를 수행하여야 한다[11]. 이에 [Fig. 15]와 같이 물류 현장 맞춤형 팔레타이징 설비가 개발된 바 있다.
낱개 핸들링 로봇은 낱개(피스) 단위의 소형 비정형 사물을 인식/피킹 하여 출고용 오더박스에 투입하는 로봇을 말한다. 핸들링 로봇 기술에 있어 가장 고난이도의 개발 특성을 가지고 있는데 기본적으로 다관절 타입을 사용 중이며, [Fig. 16]과 같이 비전을 통해 1)물성을 인식 2)물성의 형태 파악 3)파지점 도출 4)로봇 이동 및 피킹으로 구분할 수 있다. 이들 중 2) – 4)에 해당하는 프로세스가 다양한 연구를 통해 개발 중에 있다[12].
낱개 핸들링 로봇을 현장에 적용하는 데 있어서 극복해야 할 가장 중요한 요소는 다수 상품의 동시처리 능력이다. 작업자는 동시에 여러 상품을 한 번에 픽업할 수 있는 반면 로봇은 아직 한 번에 한 개의 상품만 픽업하는 방식으로 동작한다[Fig. 17]. 이를 극복하기 위해서는 보다 빠른 로봇팔과 정교한 로봇 핸드, 빠른 비전 인식, 촉각센서의 활용 등이 필요하다.
해외 유명 사례 중 하나인 Righthand Robotics社에서도 물체의 형상에 따라 2 in 1 형식의 그리퍼를 활용하여 최단시간 내 피킹을 수행하고 있다. 하지만 이 역시 모든 물성에 대한 피킹이 불가하기에 제한적인 영역에서만 상용화되었다[13].
3.4 기타 물류센터 적용 로봇
본 절에서는 앞서 언급한 이송, 피킹에 특화되어 있는 로봇 외 기타 물류 프로세스에 적용 가능한 로봇 시스템 및 보조 장치에 대해 서술한다.
택배 간선 차량의 화물 하차 작업은 작업자의 노동강도가 매우 높아 자동화에 대한 요구가 매우 높은 작업 중 하나이다.
해외에서는 상용화된 로봇 기반 하차자동화 시스템들도 있지만 박스, 마대, 파우치 등 다양한 형태의 화물이 오정렬/비정형으로 적재되어 있는 실제 택배 현장[Fig. 18]에 적용 가능한 설비는 국내외적으로 개발된 사례가 없는 상황이다.
매우 다양한 택배 화물의 형태, 크기, 재질 등에 모두 대응할 수 있는 자동화 시스템 개발을 위해서는 고난이도의 기술이 요구된다. 기본적으로 물류의 위치 및 형태 파악을 위한 비전 시스템, 인식된 형상에 대한 파지점을 판단하는 알고리즘, 제한된 구획 내에서 로봇을 효과적으로 움직이는 경로 제어, 다양한 면(Plane)에서의 피킹 및 적재를 위한 그리퍼 기술 등이 있다. 그 밖에도 하차 작업 시 화물이 무너짐에 대응 가능해야 하며 큰 기온편차 및 분진에도 강인해야 하는 등 매우 도전적인 분야이다.
일반적으로 웨어러블 로봇은 외골격 형태가 많이 알려져 있고 주로 군사목적용, 재활치료용 등으로 개발된 사례가 있다. 앞서 3.4.1의 서두에서 언급한 바와 같이 택배 하차와 같이 노동강도 높은 현장에서 웨어러블 로봇에 대한 필요성 및 활용성은 매우 높지만 외골격 형태의 웨어러블 로봇은 착용성, 자유도 및 가동시간 등의 문제로 실제 활용은 어려운 상황이다.
물류 현장에서 웨어러블 슈트의 효과적인 활용을 위해서는 1) 착용성, 2) 근력보조, 3) 유지보수 용이성 등이 전제되어야 한다. 이러한 이유로 무전원 방식의 웨어러블 슈트가 효율적이라 할 수 있다. 특히 물류 프로세스 별로 작업자의 주된 움직임이 정해져 있어 특정 움직임에 대한 근력 보조력이 높아야 한다.
최근 국내에서도 택배 하차작업과 다양한 화물 이재/적재에 활용 가능한 경량 무전원 웨어러블 슈트의 시범 적용이 진행되고 있다[Fig. 19]. 작업자가 혼자 쉽게 착용할 수 있고 착용에 따른 이질감이 적으며 효과적인 근력 지원을 제공하는 것이 관건이다.
4. 로봇의 적용으로 변화되는 미래 물류센터
앞서 3장에서 언급된 바와 같이 다양한 물류 로봇은 저마다의 특징과 장단점을 가지고 있다. 그러므로 물류센터 내 로봇 적용에도 적절한 기술과 운영방법을 찾아 효율성을 높이는 접근이 필요하다[Fig. 20]. 대표적으로 풀필먼트 센터의 경우, 처리해야하는 SKU와 주문량에 따라 가장 적합한 자동화 솔루션의 형태가 달라지게 된다. SKU와 주문량이 많을 때는 AGV, AMR과 같은 로봇을 통해 복잡한 주문을 처리하고 작업자의 이동을 최소화하는 것이 유리하지만, 주문량 또는 SKU수가 적은 경우 오히려 피킹 카트를 끌고 다니는 수작업이 효율적이다.
향후 지속적인 이커머스 성장에 따라 물류센터는 더욱 대형화되고, 그에 적합한 다양한 로봇들이 활용될 것으로 전망된다[Fig. 21]. 입고, 보관, 피킹(박스/낱개), 상하차 등 물류센터 프로세스의 전 영역에 걸쳐 물류로봇이 적용되어 작업 생산성을 높이고, 작업량을 향상시키며, 서비스 품질을 높이는 효과를 나타낼 것이다.
물류 자동화를 위해 로봇을 적용하는 데 있어서 반드시 고려해야 하는 것은 단위 공정의 자동화에 집중할 것이 아니라 전체적인 프로세스의 개선 관점에서 봐야 한다는 것이다. 아직 물류 현장에는 사람이 해야 하는 작업이 상당히 많다. 기존 물류 센터의 PI(프로세스 혁신) 활동을 진행하면서 각종 로봇을 활용한 자동화를 시도하는데 자동화 프로세스의 앞뒤 프로세스와 연결성을 충분히 고려하지 못해 초기에 목표했던 생산성이 나오지 않는 경우도 있다. 그래서, 새로운 물류 센터를 기획하면서 프로세스 설계와 자동화 시스템 설계가 같이 진행될 때 결과가 더욱 좋게 나오는 것을 경험할 수 있다.
5. 결 론
이 논문에서는 CL, 택배, 풀필먼트의 3가지 물류 서비스의 특징을 요약했고, 확산되고 있는 물류 로봇을 이송 자동화 로봇, 핸들링 로봇과 기타 로봇의 3가지로 나누어 그 특징과 적용 현황을 정리하였다.
물류 현장의 자동화는 근래 큰 변화의 모습을 보이고 있다. 불과 4, 5년전에는 고정식 설비를 중심으로 한 물류 자동화 솔루션이 대부분이었지만, 최근 2, 3년에는 확대되는 이커머스로 인한 물동량 변동과 다양한 불확실성으로 인해 유연성과 확장성이 높은 로봇 활용 자동화로 그 방향이 바뀌었다. 특히, AGV는 매년 생산성이 더욱 높아지고 처리 능력이 개선된 새로운 시스템이 출시되고 있다.
물류 기업에게 물류 현장의 자동화는 향후 지속성장을 위해 반드시 필요한 경쟁력의 원천이 되어가고 있다. 또한, 물류는 우리가 살아가는데 필수적인 서비스로 자리매김하고 있다. 우리의 삶의 질을 높이는 데에도 물류 자동화는 매우 중요한 신기술 적용 분야가 되었다. 앞으로 더욱 많은 로봇 신기술이 물류 현장에 적용되어 각종 자동화의 난제를 해결할 필요가 있다.
References
-
B. P. Amiruddin and D. R. Romdhony, “A Study on Application of Automation Technology in Logistics and Its Effect on E-Commerce,” 2020, [Online], https://engrxiv.org/preprint/download/942/2046/1452, .
[https://doi.org/10.31224/osf.io/vs9yg]
- NFI to Deploy Boston Dynamics’ Stretch Robot, [Online], https://www.truckinginfo.com/10180435/nfi-to-deploy-boston-dynamics-stretch-robot, , Accessed: Aug, 12, 2022.
- K. C. You, K. S. Kang, and S. C. Rim, “Productivity comparison between DPS and DAS for optimal order picking system design of distribution centers,” KCSM, vol. 12, no 2, pp. 111-120, [Online], https://www.kci.go.kr/kciportal/ci/sereArticleSearch/ciSereArtiView.kci?sereArticleSearchBean.artiId=ART001709624, ./
-
J. T. Li and H. J. Liu, “Design optimization of amazon robotics,” Automation, Control and Intelligent Systems, vol. 4, no. 2, pp. 48-52, April, 2016, [Online], https://www.sciencepublishinggroup.com/journal/paperinfo?journalid=134&paperId=10014718, .
[https://doi.org/10.11648/j.acis.20160402.17]
- K. Lopienski, Warehouse Picking Strategies to Improve Order Fulfillment in the Warehouse, [Online], https://www.shipbob.com/blog/warehouse-picking, , Accessed: Aug, 12, 2022.
- AGV-AMR Market to Exceed $18 Billion by 2027, [Online], https://www.thelogisticsiq.com/research/automated-guided-vehicles-agv-market, /, Accessed: Aug, 12, 2022.
-
R. D. Andrea, “Guest Editorial: A Revolution in the Warehouse: A Retrospective on Kiva Systems and the Grand Challenges Ahead,” Transactions on Automation Science and Engineering, vol. 9, no. 4, pp. 638-639, Oct. 2012.
[https://doi.org/10.1109/TASE.2012.2214676]
- Vision system achieves 100% error-free picking, [Online], https://warehousenews.co.uk/2011/09/vision-system-achieves-100-error-free-picking, /, Accessed: Aug, 12, 2022.
-
M. Beckschäfer, S. Malberg, K. Tierney, and C. Weskamp, “Simulating Storage Policies for an Automated Grid-Based Warehouse System,” International Conference on Computational Logistics, vol. 10572, Sep, 2017.
[https://doi.org/10.1007/978-3-319-68496-3_31]
- R. Caccavale, P. Arpenti1, G. Paduano1, A. Fontanellli1, V. Lippiello1, L. Villani1, and B. Siciliano, “A Flexible Robotic Depalletizing System for Supermarket Logistics,” 2020 IEEE/RSJ International Conference on Intelligent Robots and Systems (IROS), Las Vegas, NV, USA, 2020, [Online], http://ras.papercept.net/images/temp/IROS/files/2477.pdf, .
-
R. Krug, T. Stoyanov, V. Tincani, H. Andersson, R. Mosberger, G. Fantoni, and A. J. Lilienthal, “The Next Step in Robot Commissioning: Autonomous Picking and Palletizing,” IEEE Robotics and Automation Letters, vol. 1, no. 1, pp. 546-553, Jan. 2016.
[https://doi.org/10.1109/LRA.2016.2519944]
-
G. A. Fontanelli, G. Paduano, R. Caccavale, P. Arpenti, V. Lippiello, L. Villani, and B. Siciliano, “A Reconfigurable Gripper for Robotic Autonomous Depalletizing in Supermarket Logistics,” IEEE Robotics and Automation Letters, vol. 5, no. 3, pp. 4612-4617, July 2020.
[https://doi.org/10.1109/LRA.2020.3003283]
-
R. Hodson, “How robots are grasping the art of gripping.” Nature, vol. 557, pp. S23-S25, May, 2018.
[https://doi.org/10.1038/d41586-018-05093-1]
- S. H. Kim, “CJ Logistics Develop and Apply Wearable Robotic Suits to Support On-site Workers,” Metro, [Online] https://www.metroseoul.co.kr/article/20220728500028, , Accessed: 10, 21, 2022.
2011 서울과학기술대학교 기계공학과(학사)
2013 서울과학기술대학교 기계공학과(석사)
2017 서울과학기술대학교 나노IT 융합대학원(박사)
2017~현재 CJ대한통운 TES물류기술연구소 책임연구원
관심분야: Logistics Automation, Smart Warehouse, Handling automation, Manipulation
2009 한양대학교 기계공학부(학사)
2011 한양대학교 기계공학과(석사)
2015 한양대학교 기계공학과(박사)
2015~2020 한국산업기술평가관리원 선임연구원
2020~현재 CJ대한통운 TES물류기술연구소 선행기술팀장
관심분야: Logistics Robot, Logistics Automation Technology, Autonomous Vehicle
2013 한양대학교 교통시스템공학과(공학학사)
2012~현재 CJ대한통운 TES물류기술연구소 책임
관심분야: Digital Transformation Strategy, Logistics Automation Technology, Technology Planning
2002 아주대학교 산업공학(학사)
2004 아주대학교 기업물류(석사)
2020~현재 CJ대한통운 TES물류기술연구소 미래기술담당
관심분야: Logistics Robot, Logistics Automation Technology, Supply Chain Optimization
1987 서울대학교 기계설계학(학사)
1989 KAIST 생산공학(석사)
2004 KAIST 기계공학(박사)
2020~현재 CJ대한통운 TES물류기술연구소장
관심분야: Robotic Manipulation, Mobile Robot, Logistics Automation